Здесь мы собираем самые интересные статьи, интервью, репортажи и многое другое. Зарегистрируйте личный кабинет и вам будет открыт полный доступ
Когда гибкость заложена в саму основу оборудования
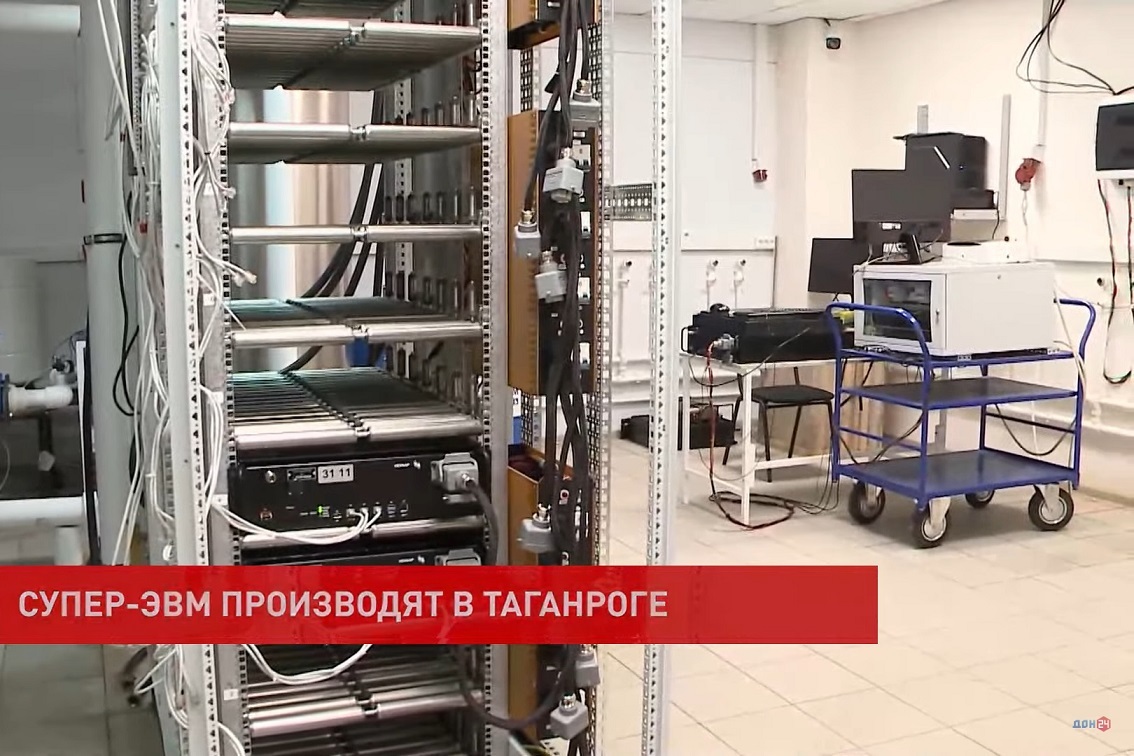
В конце прошлого года Научно-исследовательский центр супер-ЭВМ и нейрокомпьютеров (НИЦ СЭ и НК), расположенный в Таганроге и специализирующийся на разработке сложных вычислительных устройств, завершил проект по модернизации своего сборочного участка, фактически преобразовав его из площадки для изготовления прототипов и опытных партий в полноценное серийное производство. Новое оборудование приобреталось и вводилось в строй постепенно, и процесс перевооружения занял несколько лет. В результате, на предприятии были внедрены установка отмывки печатных плат, высокотехнологичный ремонтный центр, система АОИ и новая сборочная линия на основе оборудования компаний Europlacer и SMT Maschinen und Vertriebs GmbH & Co. KG (SMT Wertheim).
О том, какие этапы включал проект, как выбиралось оборудование и что изменилось с его приобретением, нам рассказали представители НИЦ СЭ и НК, а также компании «Новые Технологии», выступившей в роли поставщика оборудования в этом проекте.
ВЗГЛЯД ПОСТАВЩИКА
Алексей Маурин, коммерческий директор ООО «Новые Технологии»: Началось всё с того, что уже много лет назад на нашем стенде на выставке ElectronTechExpo мы встретились с Сергеем Поповым, начальником цеха монтажа и ремонта печатных плат НИЦ СЭ и НК. Мы рассказали ему о нашей компании, об оборудовании, которое поставляем. По сути, это был простой подход к стенду, один из многих, которые обычно совершают посетители выставок с тем, чтобы получить как можно больше различной информации и составить общую картину. Но в процессе общения выяснилась одна деталь: оказалось, что Сергей Алексеевич обратил внимание на наш стенд благодаря тому, что у компании уже было оборудование Europlacer – автомат установки компонентов и принтер – в составе небольшой линии. Однако с учетом развития производства НИЦ СЭ и НК имеющееся оборудование уже не в полной мере отвечало потребностям предприятия.
В процессе последовавшего общения с Сергеем Алексеевичем мы составили четкое представление о том, что им было нужно для технического обновления, и смогли составить предварительный проект. Но модернизацией линии сборки предприятия мы занялись позже, а предметом первого запроса коммерческого предложения от НИЦ СЭ и НК стала система отмывки.
Денис Подольский, ведущий менеджер проектов ООО «Новые Технологии»: Мы сделали предложение для НИЦ СЭ и НК по установке струйной отмывки PSE LH5 компании Kolb Cleaning Technology GmbH, которое оказалось лучшим по сравнению с предложениями наших конкурентов как по цене, так и по техническим возможностям.
Дело в том, что изделия, которые разрабатывает НИЦ СЭ и НК, совсем непростые, в том числе с технологической точки зрения. Печатные платы изобилуют компонентами BGA с большим количеством выводов, что повышает сложность не только монтажа, но и отмывки. Предложенное нами решение позволило обеспечить высокую технологичность производства, отличный результат и удобные условия поставки.
Поставка системы отмывки PSE LH5 с привлечением лизинговой компании стала нашим первым проектом с этим заказчиком. Это было в 2014 году.
А еще через некоторое время у предприятия возникла необходимость приобретения установки для ремонта плат с BGA-компонентами. Думаю, новая заявка от НИЦ СЭ и НК была отправлена нам, потому что в процессе подготовки, поставки и пуско наладочных работ с установкой Kolb наши специалисты показали себя как профессионалы не только в постановке процесса отмывки, но и в целом в технологии сборки сложных печатных плат.
Алексей Маурин: В короткие сроки нами была решена непростая задача по организации качественного процесса отмывки изделий заказчика. И дальнейшее продолжение сотрудничества явилось результатом установившегося между нами заслуженного доверия.
Денис Подольский: Знакомиться с оборудованием представители НИЦ СЭ и НК приезжали к нам, в Санкт- Петербург, где мы организовали экскурсии на предприятия, на которых ремонтные центры уже применялись. Наши коллеги также интересовались печами оплавления: паять новые изделия в той печи, которая была в их линии, становилось всё сложнее.
Но всё же вопрос автоматизации процесса ремонта был для специалистов заказчика особенно актуален. Ведь в НИЦ СЭ и НК занимаются не только производством, но и разработкой собственных изделий. В таких условиях жизненно необходимо иметь возможность быстро собирать прототипы и вносить в них изменения. А если у вас на плате множество дорогостоящих микросхем в BGAкорпусах с парой тысяч выводов в окружении нескольких тысяч других компонентов, в том числе 0201, делать это без качественного оборудования невозможно. Поэтому решением с нашей стороны было предложение прецизионного ремонтного центра RD-500V японского производителя Den-On Instruments Co., Ltd.
По описанию конструкций их плат мы подобрали наиболее похожие образцы с точки зрения теплоемкости и состава компонентной базы и продемонстрировали на этих образцах работу оборудования в нашем технологическом центре. Коллеги из НИЦ СЭ и НК сами смогли «отремонтировать» один образец, изучили его на установке рентгеновского контроля и остались очень довольны.
Мы также воспользовались случаем и продемонстрировали работу печи от компании SMT Wertheim на таких же образцах. Но на тот момент приоритетом компании было приобретение ремонтного центра, а на модернизацию линии бюджет еще не был выделен.
Ситуация изменилась в 2018 году, когда компания получила достаточно крупные заказы. Учитывая сложность новых изделий, а также сжатые сроки исполнения, заказчик принял решение собирать часть заказов на собственной площадке в НИЦ СЭ и НК, под своим непосредственным контролем. Впоследствии оказалось, что это было очень правильное решение: заказы были выполнены в полном объеме и в установленные сроки.
Алексей Маурин: Главная задача, которую поставил перед нами заказчик, заключалась в том, чтобы новое оборудование было настолько же гибким, как и в старой линии, позволяя быстро переходить с одного изделия на другое и собирать разнообразные платы со сложными компонентами, но при этом при необходимости обеспечивало быстрое изготовление достаточно больших партий.
Для того чтобы подобрать оптимальную конфигурацию оборудования, мы выполнили компьютерное моделирование – виртуальную сборку, а также расчеты времени подготовительных операций. В качестве первого установщика был выбран компактный высокопроизводительный автомат xpii+, а второй машины – универсальный автомат iineo+ с большой базой питателей и широким спектром устанавливаемых компонентов, оба производства Europlacer (Франция). Максимальная производительность первой установки составляет более 26 тыс., а второй – 14 тыс. комп. / ч.
Виталий Авласович, руководитель сервисной службы ООО «Новые Технологии»: Замечу, что установщики Europlacer спроектированы для решения подобных задач. Обладая достаточной производительностью для целевых объемов производства заказчика, они позволяют производить изделия любой сложности и очень быстро выполнять переналадку. Сейчас многие производители установщиков, в том числе предназначенных для крупносерийного и массового производства, утверждают, что переналадка их оборудования выполняется очень быстро. Казалось бы, действительно, сейчас всё серьезное оборудование снабжено интеллектуальными питателями и программным обеспечением для оптимизации сборки.
Программирование и зарядку питателей можно выполнять вне линии, а потом просто пристыковать подкатные тележки к автомату – и всё готово.
Вот только на практике одна лишь загрузка лент в питатели и питателей в установщики компонентов может занимать дни. У Europlacer это не так.
В установщиках Europlacer гибкость обеспечивается не только и не столько дополнительными инструментами, сколько самой концепцией оборудования. Она заложена на базовом уровне. Например, зарядка 8-мм питателя занимает максимум 20 с, что раза в два меньше, чем у большинства автоматов известных производителей.
Оптимизация сборки выполняется «на лету», что позволяет изначально ставить питатели в любые позиции, а не только в указанные оптимизатором. В результате они устанавливаются быстрее, и исключается возможность ошибки. Еще один пример: автомат сам определяет высоту компонента и уровень его захвата из питателя, их не нужно закладывать в программу, а следовательно, нет необходимости измерять новый компонент или искать документацию на него, прежде чем зарядить его в питатель. Автоматизация на этом этапе экономит огромное количество времени и устраняет возможные потери компонентов при работе оборудования.
Такие особенности автоматов Europlacer сокращают само время переналадки, а не просто «прячут» его в рабочий цикл оборудования.
Решающее значение имеет количество одновременно используемых различных типов компонентов и позиций для установки питателей. Кроме того, что большое количество слотов для питателей позволяет производить любое изделие в один проход, это также значительно ускоряет переналадку.
Установщики Europlacer имеют, пожалуй, самую большую на сегодняшний момент базу питателей. У iineo+ она включает 264 позиции под 8-мм ленты и монтажный стол, на котором можно разместить более 60 номиналов без сокращения количества свободных слотов. У xpii+ позиций питателей не так много – 66, так как назначение этого установщика несколько иное, но и он также снабжен небольшим монтажным столом для установки компонентов из поддонов и россыпи.
Благодаря этим и другим преимуществам оборудования Europlacer удалось построить линию, отвечающую потребностям заказчика, на двух автоматах установки компонентов. Если бы использовались установщики другого производителя, вероятнее всего, потребовалось минимум три машины.
Денис Подольский: Стоит добавить еще про две функции автоматов Europlacer, которые оказались очень полезны для обеспечения высокого качества сборки таких сложных изделий, какие изготавливает НИЦ СЭ и НК. Первая – это базовая способность оборудования в процессе сборки проверять компланарность выводов компонентов. На практике при монтаже корпусов с большим количеством выводов и малым их шагом дефекты, связанные с небольшой деформацией вывода, представляют ощутимую проблему. Установщики Europlacer просто отбракуют компонент с таким выводом, сообщив о проблеме оператору.
Вторая функция – оснащение автоматов Europlacer модулем измерения электрических параметров чипкомпонентов. Измерение RLC-значений компонентов перед установкой на плату позволяет исключить влияние человеческого фактора, а также оперативно выявлять контрафакт.
Алексей Маурин: Практически сразу после автоматов установки компонентов НИЦ СЭ и НК заказал и новую печь, а затем – установку автоматической оптической инспекции. Всё это произошло в пределах полугода и стало самым крупным этапом перевооружения производства компании. А старый автомат мы взяли на реализацию, провели его техническое обслуживание, и эту установку приобрел еще один наш заказчик, который также выпускает сложные изделия ответственного применения. И вот уже около трех лет она работает на его производстве.
А в конце прошлого года очередной этап модернизации производства НИЦ СЭ и НК был завершен поставкой и вводом в эксплуатацию новой установки трафаретной печати серии EP710 – также от компании Europlacer. До того в линии использовался тоже достойный принтер – Speedprint SP700avi. Но старая машина проработала около 10 лет. Поэтому заказчик и принял решение о ее замене.
Помимо того, что новый принтер обладает высокой производительностью и повторяемостью, в нем может быть реализована возможность нанесения пасты методом дозирования, которая очень полезна для компании, разрабатывающей и производящей собственные изделия, поскольку это позволяет наносить пасту на прототипы без изготовления трафарета. Кроме того, с помощью этой функции можно наносить дополнительную пасту на площадки крупных компонентов, если на плате присутствуют также и миниатюрные корпуса, и трафарет большой толщины применяться не может. А на данную машину можно установить сразу два дозатора, например для паяльной пасты и клея, и дозировать паяльные материалы точками и линиями.
Процесс прохода ракеля по трафарету контролируется компьютерной системой оборудования для обеспечения равномерного усилия, чтобы получить одинаковое количество пасты на всех контактных площадках.
Отличительной особенностью принтера также является его способность поддерживать свои точностные характеристики в течение всего срока эксплуатации. Это достигается путем применения оригинальной системы видеокамер, с помощью которых принтер самостоятельно производит свою калибровку.
Кстати, при вводе в эксплуатацию был осуществлен перенос всех имевшихся у заказчика библиотек и рабочих программ на новую линию. Благодаря опыту наших инженеров и специалистов НИЦ СЭ и НК это было сделано без каких-либо проблем.
Денис Подольский: Вообще пусконаладка оборудования выполнялась очень быстро. Например, с момента, когда заказчику поступили автоматы установки компонентов, и до момента выхода первых – уже «боевых» – изделий прошло всего два дня.
Алексей Маурин: Да, действительно, специалистам НИЦ СЭ и НК и нашим инженерам удалось оперативно ввести всё оборудование в строй, чтобы как можно быстрее перейти к выпуску серийной продукции. Это было очень важно для заказчика, поскольку основная часть модернизации производства осуществлялась под конкретные заказы, для которых уже были установлены сроки выполнения.
Мы смогли сделать это благодаря совокупности факторов. Здесь дело и в оборудовании, его дружественном программном обеспечении, высоком уровне технологичности, что позволяет избежать длительного процесса подключения и настройки, и в том, что персонал НИЦ СЭ и НК уже обладал опытом работы с установками Europlacer и был хорошо знаком с технологией поверхностного монтажа сложных изделий. И без ложной скромности скажу, что не последнюю роль сыграл и профессионализм нашей команды.
Проект был действительно технически сложным, но мы его реализовали и, как видим сейчас, сделали это на высоком уровне.
ВЗГЛЯД ЗАКАЗЧИКА
Сергей Попов, начальник цеха монтажа и ремонта печатных плат ООО «Научно-исследовательский центр супер-ЭВМ и нейрокомпьютеров»: До знакомства с компанией «Новые Технологии» мы работали с другим поставщиком, который в 2010 году нам поставил линию на основе автомата Europlacer. Поставки оборудования Europlacer, скорее всего, не были основным направлением деятельности этой компании, что негативно проявилось в некоторых моментах при эксплуатации. Поэтому впоследствии мы полностью переключились на сотрудничество с «Новыми Технологиями». Специалисты нашего нового партнера не только профессионально выполняют монтаж и пусконаладку оборудования, но и обеспечивают нам необходимую и, что важно, своевременную техническую поддержку.
Но когда мы задумались о приобретении нового оборудования, мы не сразу остановили свой выбор на данной компании. Мы рассматривали в том числе вариант перехода на автоматы установки компонентов другого вендора. Не буду называть этого производителя, тем более что он создает качественное оборудование высокого технологического уровня, очень производительное. Собственно, из-за производительности мы и обратили внимание на эти автоматы.
Однако они оказались для нас менее подходящими, чем установщики Europlacer, по ряду критериев, прежде всего по гибкости. Эти автоматы не позволяли устанавливать компоненты из россыпи – а в наших условиях это важно, поскольку, к сожалению, многие отечественные производители ЭКБ не упаковывают компоненты в ленту. Работа с обрезками лент на них была очень сложной. В целом, процесс переналадки этих машин выглядел достаточно сложным в сравнении с установщиками Europlacer. Для установки определенных типоразмеров даже нужно было менять монтажную голову.
Сыграл свою роль и тот факт, что для освоения этого оборудования нам нужно было бы переучиваться, а производство – это процесс, в котором нельзя терять время. Более того, мы приобретали автоматы непосредственно перед запуском в производство ряда больших заказов и потому были особенно ограничены во времени.
Оборудование Europlacer нам уже было знакомо, хотя первое производство у нас было небольшим, в линии тогда стоял только один автомат. Кроме того, мы многократно видели эти установщики на различных выставках, таких как ElectronTechExpo, где мы и познакомились с «Новыми Технологиями». Мы понимали, насколько оборудование Europlacer гибкое и универсальное, поэтому в результате для перевооружения производства мы выбрали именно его.
Для нас было важно, чтобы оборудование позволяло монтировать широкий спектр компонентов – от миниатюрных чип-корпусов до больших микросхем, и чтобы оно позволяло быстро переходить на изготовление нового изделия. Эти возможности как раз отличают автоматы Europlacer. Кроме того, эти машины просты в обслуживании: если что-то и выходит из строя, как правило, можно произвести ремонт своими силами. Этому помогает и подробная документация, которая поставляется вместе с данным оборудованием.
Артём Шевченко, технолог 1-й категории ООО «Научно-исследовательский центр супер-ЭВМ и нейрокомпьютеров»: Но перевооружение нашего производства во взаимодействии с «Новыми Технологиями» началось не с автоматов установки компонентов. Этому предшествовало приобретение системы отмывки и ремонтного центра – высокотехнологичной установки, которая позволяет демонтировать и устанавливать на платы сложные компоненты, которые в больших количествах встречаются в наших изделиях.
Наша компания занимается разработкой и изготовлением сложных вычислительных устройств на основе ПЛИС, которых на плате может быть до 16 шт. На платы, которые могут состоять из 24 слоев, устанавливается несколько тысяч компонентов. Сами ПЛИС – это микросхемы в корпусе BGA, которые могут насчитывать порядка 2 000 выводов. Иногда на платах присутствуют передовые процессоры – очень «капризные» компоненты, которые предъявляют крайне высокие требования к техпроцессу в отношении как позиционирования, так и термопрофиля пайки. Поэтому для ремонта наших изделий требуется современное высокотехнологичное оборудование, каковым является приобретенный нами ремонтный центр.
И конечно, к оборудованию в сборочной линии также предъявляются очень высокие требования. На старой линии мы собирали небольшие партии и опытные образцы, но для изготовления более крупных партий требовалось новое, более производительное, оборудование. Кроме того, хотя мы и справлялись с пайкой наших изделий в старой печи, приходилось долго, иногда несколько дней, подбирать термопрофиль. А термопрофилирование мы выполняем для каждого изделия индивидуально. Порой мы были вынуждены прибегать к различным ухищрениям, вплоть до экранирования отдельных зон и компонентов, чтобы их не перегреть.
Сергей Попов: Процесс перевооружения происходил в течение нескольких лет. Глубокая модернизация потребовала бы на длительный период полностью остановить производство, что, конечно, абсолютно неприемлемо. Простой линии в два-три месяца серьезно усложнил бы производственные планы, возникли бы риски срыва сроков проектов.
Кроме того, не стоит забывать и о финансовой составляющей. Наша компания – частная, где успех в том числе зависит от точного экономического планирования расходов, а для модернизации производства нужны значительные средства, которые не всегда целесообразно выделять одномоментно.
В 2018 году мы получили ряд крупных заказов, что в значительной мере способствовало более интенсивному обновлению парка производственного оборудования, в том числе и приобретению новых автоматов установки компонентов, печи, а также системы АОИ. Это решение было принято исходя не только из потребности в более современном оборудовании, но и с расчетом на увеличение объемов производства в перспективе.
На рубеже 2018–2019 годов мы приобрели и вместе с «Новыми Технологиями» ввели в строй два установщика: высокопроизводительный двухбалочный автомат xpii+ с двумя монтажными головами Tornado по 12 захватов на каждой и универсальную машину iineo+, которая монтирует широкий спектр компонентов, включая ПЛИС и процессоры.
Артём Шевченко: Ввести в строй эти установщики получилось всего за два дня. Еще в процессе пусконаладки мы начали собирать изделия для текущих заказов. Представьте себе: еще вчера оборудование расставлялось подъемниками, а сегодня уже выпускает продукцию, которая будет отгружена заказчику.
Это получилось за счет того, что мы уже были знакомы с оборудованием Europlacer, умели работать с его программным обеспечением, то есть сразу знали, что делать. И конечно, нужно отдать должное специалистам «Новых Технологий», которые не только быстро выполнили пусконаладку, но и помогли нам оперативно конвертировать рабочие программы.
Отмечу также, что эти автоматы оправдали наши ожидания в плане простоты переналадки. Вся подготовка производства нового изделия выполняется полуавтоматически, рабочие программы создаются путем конвертации данных из САПР, программирование установок и питателей проводится на отдельном рабочем месте, подключенном к тому же серверу, что и оба автомата. Еще одна приятная деталь: оптимизатор позволяет очень точно распределить установку компонентов между двумя машинами с тем, чтобы одна из них не ждала другую.
Сергей Попов: Чуть позже мы установили и новую печь SMT Wertheim, полностью устранившую необходимость в тех трюках, которые приходилось делать на старой установке. Благодаря превосходным характеристикам по теплопередаче печи от SMT теперь мы подбираем профиль для любой, даже самой сложной, платы меньше чем за полсмены. Вообще, печь очень стабильная, она обеспечивает высокую степень равномерности прогрева плат, температура в ней не меняется в зависимости от сезона, как это было в старой печи.
Кстати, поначалу для нас удивительно было то, что эта установка, содержащая даже меньше зон нагрева, чем старая печь, обеспечивает гораздо лучшие результаты пайки. Казалось странным: у нас такие сложные изделия, а печь всего лишь пятизонная. Оказалось, что в современном оборудовании принципиально не количество нагревателей, а длина туннеля нагрева и качественная теплопередача. А то, что у печи больше зон, совершенно не означает, что она позволит выстраивать более подходящий профиль и обеспечит высокое качество пайки.
В конце прошлого года мы закончили обновление сборочного производства внедрением нового принтера Europlacer EP710. Теперь вся наша линия поверхностного монтажа состоит из нового оборудования, ни одной старой установки в ней не осталось.
Когда мы решили приобрести новый принтер, главной задачей мы видели просто обновление установки для этой операции, поскольку ей уже было около 10 лет. С ней периодически возникали те или иные проблемы, какие-то узлы приходилось менять, но в целом она справлялась со своими задачами. Однако, когда мы начали работать на новом принтере, мы ощутили, насколько он быстрее и точнее.
У его производителя был ролик, в котором демонстрировалась точность этой установки с помощью следующего эксперимента. Выполнялось нанесение пасты на плату, а потом та же плата – уже с нанесенной пастой – вновь загружалась в принтер, и он снова наносил на нее пасту. Это повторялось несколько раз. И отпечатки при этом не размазывались и не смещались; они были точно такими, как если бы печать выполнялась лишь единожды. То есть принтер настолько хорошо компенсирует смещение платы, которое неизбежно возникает при каждой загрузке, что трафарет ложится апертурами точно на нанесенные отпечатки.
Так вот, мы засомневались в правдивости ролика и решили повторить этот эксперимент. И оказалось, что ролик не обманывал: в нашем эксперименте мы получили такой же, стопроцентный, результат.
Резюмируя, мы очень довольны модернизацией нашего производства. Этот проект был выполнен практически идеально; если проблемы и возникали, то они были мелкими и быстро решались, в том числе благодаря профессионализму специалистов «Новых Технологий». Про эту компанию могу сказать, что она способна решать очень широкий спектр задач в области поставки оборудования и постановки техпроцессов – от ремонта и отмывки до высокотехнологичных линий для серийного производства. Чувствуется, она работает очень слаженно, как единая команда.
Материал подготовлен Ю. С. Ковалевским.
Статья впервые опубликована в журнале "ЭЛЕКТРОНИКА: НТБ" № 3 за 2022 год.
Понравилась статья? Поставьте лайк