Здесь мы собираем самые интересные статьи, интервью, репортажи и многое другое.
«Домашняя» MES-система: на НПО «ЦТС» разработали и внедрили собственный программный комплекс для оперативного управления производством
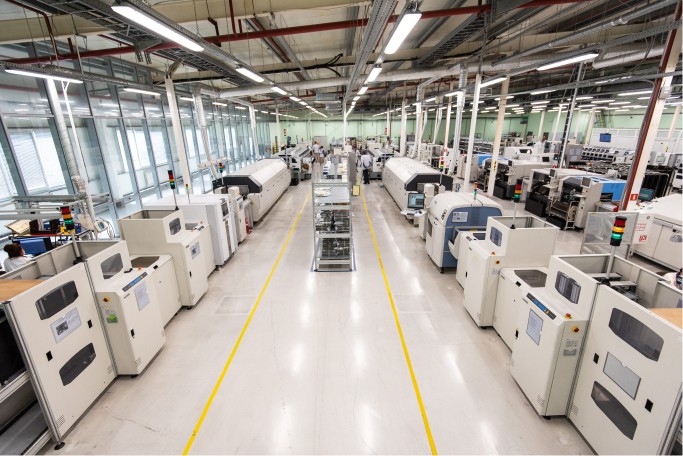
На заводе АО «НПО «Цифровые Телевизионные Системы» (в составе инновационного кластера «Технополис GS» в г. Гусеве Калининградской области) действует собственная MES-система, разработанная силами ИТ-специалистов предприятия. Она обеспечивает полную прослеживаемость производственных процессов и позволяет оперативно передавать заказчикам информацию об изделиях. Об опыте разработки и реализации системы рассказывает технический директор «ЦТС» Станислав Лишик.
MES-система (manufacturing execution system, с англ. — производственная исполнительная система) — это программный комплекс, который используется для автоматизации и контроля производственной деятельности. Он позволяет управлять процессами в режиме реального времени и сохраняет информацию обо всех этапах производства, вплоть до выпуска готовой продукции. На русском языке вместо MES часто употребляется аббревиатура АСОУП — автоматизированная система оперативного управления производством.
С чем была связана потребность в собственной системе?
Любой системе нужно время для адаптации под требования конкретного завода или группы предприятий, существующих внутренних процессов. Когда мы создаем систему под себя с нуля, мы избегаем этих промежуточных этапов и сразу создаем именно то, что нужно нам, и в результате получаем отчетность в нужном виде. Наша система гибка, мы можем легко и достаточно быстро ее доработать без существенных инвестиций. Все крупные зарубежные производственные компании пишут собственные MES-системы, в том числе и те, которые приходят в Россию. Если говорить о российской электронной отрасли, то наше решение, пожалуй, единственное.
В чем ключевые особенности системы «ЦТС»?
Прежде всего, это прослеживаемость на всех этапах производства. Таким может похвастаться не каждый российский производитель электроники. Наша система позволяет отследить каждое изделие на всех этапах: сбора заказа, комплектации, поверхностного и выводного монтажа, сборки и тестирования. Мы видим весь процесс целиком. Это реализовано с помощью QR-кодов, которые мы гравируем на платах, а также штрих-кодов на компонентах. Мы знаем, в какой день, из каких материалов, какой сменой, какими операторами, на какой линии и каким оборудованием было собрано каждое изделие. Как оно прошло весь цикл сборки, были ли какие-то ошибки или нет, ремонтировалось ли изделие, проходило ли оно выборочный выходной контроль, блокировалось или нет и т. д. — нам известна вся история изделия по его серийному номеру. Благодаря этому любой заказчик может эту информацию оперативно получить. Если нам заказчик сообщает, что у него возникли какие-то проблемы с изделием, либо он от своего поставщика узнал, что была проблема с компонентами, мы можем определить весь список изделий, в которых установлены эти компоненты, когда они собирались, что из продукции осталось на складе, а что уже отгрузили и т. д.
Еще одно важное преимущество — сканируя штрих-код, мы проверяем правильность компонента, что особенно важно в крупносерийном производстве. Например, один заказ составляет условно 10—15 тысяч плат, и если мы поставили неправильный компонент, то вся партия уходит на ремонт. Это своеобразная защита от дурака. Мы знаем, что поставлен правильный компонент, что неотремонтированное изделие не было упаковано и отправлено заказчику.
Третий фактор — быстрота реакции на проблемы, которые возникают. Вся информация загружена в систему, везде висят дашборды, которые выводят информацию о заказе, производительности по цехам, на каком этапе сборке у нас находится тот или иной заказ, отстаем мы от плана или нет, какой у нас процент брака на разных участках — мы все это можем видеть в реальном времени и оперативно реагировать. Сейчас отчеты отправляются каждые 2 часа, но это все настраиваемо.
Какую платформу и язык программирования вы использовали для написания системы, опирались ли вы на опыт других крупных производственных компаний?
Мы начинали писать все на Visual Basic в Visual Studio, используя Windows Forms, затем плавно перешли на C# в тех же Forms, сейчас идем дальше и часть приложении перевели с Forms на ASP.NET. В части хранения данных используем MS SQL, так как она уже стояла у нас для других задач. Параллельно данные с оборудования собираем из Oracle, SQLite, из файлов .mdb (Access).
Опыт других компании мы не изучали, не было возможности; может, оно и к лучшему. Какие данные собирать и анализировать, отображать — было самим понятно, это естественная потребность любого производства.
Сколько инвестировано в разработку системы и насколько выгоднее создавать самим, чем приобретать и внедрять стороннюю систему?
Инвестиции — это только зарплата наших специалистов, развивающих систему, — в команде 4 человека. Готовая же система под ключ может стоить полмиллиона долларов, плюс неминуемые ежегодные затраты под «затачивание» системы под пожелания клиента.
С какими проблемами столкнулись при разработке и внедрении и что еще планируете реализовать?
Конкретных серьезных проблем не было, но не всегда все, что мы планируем, получается разрабатывать и внедрять в желаемые сроки. Но мы учимся на своих ошибках.
Планов много, но в ближайшее время хотим реализовать процесс прослеживаемости параметров для каждой платы, а также автоматическую систему регистрации перемещения материалов между цехами на базе RFID-меток.
В каком виде получает отчетность производство, возможна ли интеграция с CRM-системой?
Все отчеты приходят по почте. Также все данные в режиме реального времени отображаются на дашбордах, которые находятся в офисных помещениях производства.
Интеграция с CRM-системой возможна, но мы пока глубоко не занимались этим вопросом. Сейчас часть данных системы доступна клиентам в их личном кабинете на нашем сайте.
Как используются данные, которые собирает и накапливает система?
Все необходимые данные анализируются специалистами производства. Мы сохраняем всю информацию о проблемах, ошибках, настройках и параметрах системы. Это позволяет нам прогнозировать выпуск продукции с точки зрения контроля качества. Например, если мы собираем материнские платы одного типа, то можем прогнозировать уровень брака и продуктивность, спланировать производство и поработать с потенциальными проблемами. Также мы можем вести базовую аналитику по разбросу параметров.
В чем выражается эффект от внедрения системы и является ли ее наличие преимуществом для клиентов при выборе производственной площадки для размещения заказа?
В первую очередь, эффект от внедрения системы отражается на качестве производимой продукции. Выход годных изделий с первого предъявления вырос в среднем на 1—2 % благодаря тому, что система немедленно «подсвечивает» все проблемы и не позволяет продолжать производство с неудовлетворительными показателями.
Однозначно, MES-система — это преимущество для всех сторон. Клиенты рассчитывают, что статус выполнения их заказа всегда будет доступен для них в режиме онлайн, что, в свою очередь, позволяет им более точно прогнозировать доставку конечного продукта до своих клиентов, а также быть уверенным в качестве поставляемой продукции.
Понравилась статья? Поставьте лайк