Здесь мы собираем самые интересные статьи, интервью, репортажи и многое другое. Зарегистрируйте личный кабинет и вам будет открыт полный доступ
Формирование микровыводов припоя на уровне пластины
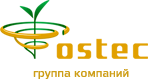
Александр Скупов materials@ostec-group.ru
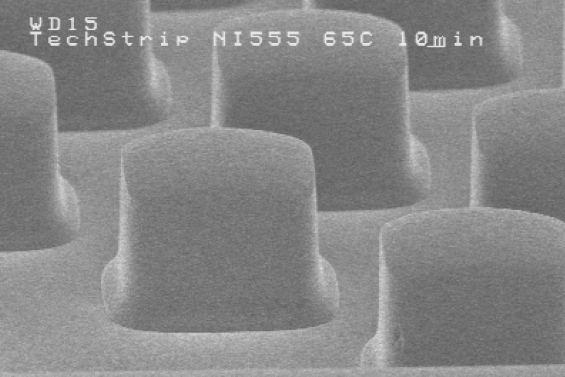
В статье приведён обзор технологий и материалов, применяемых для формирования столбиковых выводов на полупроводниковых пластинах при производстве микросхем.
Введение
Разварка с помощью проволоки из Al, Au или Cu долгое время являлась наиболее популярным методом формирования электрических соединений между контактными площадками кристалла полупроводниковой микросхемы и выводами корпуса либо контактными площадками печатной платы. Такой способ надёжен и прост, но в ряде случаев становится ограниченно пригодным для современных микросхем [1].
Если необходимо, чтобы размеры микросхемы в корпусе не превышали (или незначительно превышали) размеры её кристалла (chip scale packaging), то реализовать такие требования при проволочной разварке невозможно. В применениях, где требуется высокая скорость обработки сигнала и максимально возможная эффективность потребления энергии, проволочная разварка нежелательна из-за больших значений паразитных индуктивностей, сопротивлений и ёмкостей. Также разварка проволокой имеет ограниченную применимость в методах корпусирования 2,5D и 3D (chip-to-wafer, chip-to-chip, stacked chip), к которым сейчас стремится мировая микроэлектроника.
В качестве альтернативного метода соединения кристалла с контактными площадками корпуса или платы применяются столбиковые либо шариковые выводы. Кристалл в данном случае монтируется лицевой стороной к подложке (flip chip) либо обычным способом, но со сквозными выводами TSV (through silicon vias). Такой способ монтажа позволяет распределить выводы по всей поверхности кристалла микросхемы, существенно экономя площадь конечного устройства по сравнению с разваркой проволокой. Также flip-chip обеспечивает наилучший отвод тепла от микросхемы, поскольку радиатор можно размещать непосредственно на обратной стороне кристалла.
Формирование выводов для flip-chip – более сложный и многоэтапный технологический процесс по сравнению с разваркой проволокой. Для его реализации и получения качественных и надёжных электрических соединений на уровне пластины необходим правильный выбор материалов – резистов, диэлектриков, систем металлизации, флюсов для оплавления припоя, химии для осаждения и отмывки.
Технологический процесс и материалы
Технологический маршрут формирования выводов на поверхности кристалла показан на рис. 1. Выводы формируются на полупроводниковой пластине, прошедшей все этапы формирования металлизации (BEOL – back end of line) с верхним слоем диэлектрической пассивации и вскрытыми в нём контактными площадками.
Рисунок 1 Общий технологический маршрут формирования выводов для монтажа перевёрнутого кристалла
На первом этапе маршрута (рис. 1а) происходит формирование зародышевого слоя металла (seed layer), который наносится методом напыления, конечная толщина слоя составляет сотни нанометров. В зависимости от материала контактной площадки при напылении используются диффузионные барьеры из Ni, Cr, Ti, W либо комбинации этих материалов.
Далее выполняется литография (рис. 1б) для формирования топологии выводов. Если по какой-то причине следует изменить расположение контактов на пластине, то перед этим процессом проводят одну или несколько литографий для формирования линий металла (RDL – redistribution layer). Для литографии используются фоторезисты, образующие плёнки толщиной 10-20 мкм.
На третьем этапе формируется металл вывода (рис. 1в). Это могут быть свинцовосодержащие сплавы (PbSn), бессвинцовые припои (Sn-Ag-Cu, Sn-Ag, Au-Sn). Металлизация происходит с помощью гальванического осаждения. Поскольку пластина покрыта зародышевым слоем, металл осаждается только внутри проявленных областей фоторезиста. Сплав из нескольких составляющих получают последовательным осаждением разных слоёв с тщательно рассчитанной толщиной. Для гальванического осаждения коммерчески доступны специальные, готовые к применению растворы (например, серия растворов Elevate от компании Technic).
При непосредственном гальваническом осаждении припоя на зародышевый слой конечный диаметр выводов после осаждения составляет 75-200 мкм. В этом случае шаг между выводами составляет 150-400 мкм. Для уменьшения шага перед формированием припоя гальванически осаждают толстый слой меди. В результате получаются столбики из меди (copper pillar), на которые впоследствии осаждают слои припоя значительно меньшей толщины (рис. 2). При таком подходе шаг между выводами можно уменьшить до 20-40 мкм [2]. Всю последовательность слоёв, лежащих между металлом контактной площадки и припоем, называют промежуточной металлургией или металлизацией (UBM – under bump metallization, metallurgy).
Рисунок 2 Уменьшение размера выводов и шага между ними при использовании медных столбиков.
На последнем этапе формирования выводов происходит снятие фоторезиста (рис. 1г) и жидкостное травление зародышевого слоя (рис. 1д). На финальном этапе – нанесение флюса и оплавление припоя с последующей отмывкой пластины от остатков флюса (рис. 1е). После проделанных процедур пластина передаётся на следующий этап общего технологического маршрута для тестирования и разделения на кристаллы.
Выбор фоторезистов для гальванического осаждения металла выводов
При выборе фоторезиста для процесса гальванического осаждения есть пять основных требований:
- возможность экспонирования плёнок толщиной 10-20 мкм;
- высокая контрастность;
- высокая адгезия к металлу зародышевого слоя;
- стойкость к гальваническим растворам;
- снятие в растворах, не агрессивных к металлу выводов.
Универсальные резисты, используемые для производства микросхем, как правило, не подходят для процесса гальванического осаждения. Это связано с тем, что они рассчитаны на малые толщины плёнок (1-5 мкм) и выделяют азот при экспонировании больших толщин [3]. Сегодня на рынке доступно множество как позитивных, так и негативных резистов, пригодных или специально разработанных для процесса гальванического осаждения (таблица 1).
Таблица 1 Резисты для гальванического осаждения
Негативные резисты серии AZ 15nXT и 40 XT являются химически усиленными, AZ 125 nXT – фотополимером. Эти резисты позиционируются производителем как материалы, специально разработанные для формирования выводов на пластине. Среди материалов других марок одним из подходящих для этих целей является химически усиленный негативный резист AR-N 4400.
В качестве позитивных резистов для процесса гальванического осаждения меди и припоев специально разработаны серии резистов AZ 4500 и AZ 9200. Также для этой задачи подходят AR-P 3200 и MEGAPOSIT SPR-220. Все они обладают устойчивостью к умеренно щелочным и кислым средам, используемым для гальванического осаждения металлов.
Для снятия резистов после осаждения металла нельзя использовать реагенты, содержащие тетраметиламмония гидроксид (ТМАГ) и некоторые амины из-за их коррозионного действия на металлы. Как правило, снятие позитивных фоторезистов после гальванического осаждения не представляет каких-либо сложностей в смесях органических растворителей (ДМФА, NMP и их менее токсичные альтернативы, DMSO).
Однако снятие негативных резистов может вызывать сложности, поскольку эти материалы имеют бóльшую степень сшивки по сравнению с позитивными резистами. Для их снятия разработан специальный сниматель TechniStrip NI 555, который растворяет резист без остатка, не повреждая металлизацию. В качестве примера на рис. 3 показано снятие AZ 15nXT после формирования столбиков из меди [4].
Рисунок 3 Медные столбики до (а) и после снятия резиста AZ 15nXT (б) с помощью TechniStrip NI 555
Оплавление припоя. Флюсы
Оплавление припоя после удаления фоторезиста необходимо для формирования вывода, пригодного для дальнейшего монтажа кристалла на подложку при сборке в корпус или на плату. Перед оплавлением на поверхность пластины наносится флюс, который обеспечивает удаление оксидов металлов во время оплавления. Для применения на уровне полупроводниковой пластины компанией Indium были разработаны специальные флюсы с высокой чистотой и оптимальной вязкостью [5]. Некоторые свойства этих материалов приведены в таблице 2.
Таблица 2 Флюсы компании Indium для оплавления припоя на пластине
Нанесение флюса выполняется либо на центрифуге при 15-800 об./мин., либо с помощью распыления. Также существуют флюсы, пригодные для нанесения погружением (например, Indium 5 SLC). Очень важно, чтобы толщина нанесённого флюса превышала высоту выводов из припоя. В противном случае будут проявляться дефекты, связанные с неполным смачиванием поверхности припоя.
Нанесение флюса на центрифуге – самый распространённый метод. Зависимость толщины плёнки флюса от скорости вращения центрифуги иллюстрируется на рис. 4. Во многом процесс сходен с нанесением фоторезиста, но существует одна особенность. Даже при том, что вязкость флюса сравнима с вязкостью фоторезиста, динамики их нанесения отличаются. В флюсах применяются растворители с низкой скоростью испарения, поэтому они будут медленно испаряться, а сам флюс будет дольше сохранять способность растекаться по пластине. Такое поведение материала приводит к тому, что при длительном времени вращения он перетекает к краям, в результате чего в центре его толщина будет меньше, чем по краям. Соответственно, в отличие от нанесения фоторезиста, при центрифугировании флюса необходимо уменьшать время вращения.
Рисунок 4 Зависимость толщины флюса от скорости вращения центрифуги для некоторых продуктов компании Indium
Оплавление припоя выполняется в атмосфере азота или формиргаза. Максимально допустимое содержание кислорода в атмосфере печи составляет 20 ppm. Нагрев и охлаждение пластины осуществляется по термопрофилю, пример которого приведён на рис. 5.
Рисунок 5 Типичный вид термопрофиля при оплавлении припоя на пластине
Для удаления флюсов используются специальные отмывочные жидкости (например, Zestron FA+, Vigon A201, Vigon N600). Существуют флюсы, смываемые в деионизованной воде (например, WS 3401, 3541). Пример шарикового вывода на кристалле после оплавления припоя и отмывки остатков флюса приведён на рис. 6.
Рисунок 6 Медный столбик с оплавленным припоем после отмывки остатков флюса
Заключение
С увеличением производительности микросхем, ростом числа вводов/выводов, уменьшением топологических норм и увеличением мощности устройств для последующего монтажа кристалла на замену проволочной разварке приходят сформированные на уровне пластины выводы из припоя. Такая технология несёт очевидные преимущества:
- экономное использование площади кристалла;
- возможность эффективного отвода тепла через обратную сторону кристалла;
- уменьшение паразитных индуктивностей, сопротивлений и ёмкостей за счёт уменьшения длины и площади проводников;
- возможность простой адаптации к технологиям 3D- и 2,5D-сборок.
Технология формирования выводов припоя намного сложнее проволочной разварки – она требует проведения процессов напыления, фотолитографии, гальванического осаждения, нанесения и оплавления флюса. Правильный выбор технологических материалов для каждого этапа исключительно важен для получения надёжных и качественных выводов.
Группа компаний Остек сотрудничает с производителями материалов для наиболее критичных этапов процесса: напыления, фотолитографии, оплавления припоя. Специалисты Остека готовы оказать технологическую поддержку в области применения материалов для создания выводов припоя на уровне пластины, совместно с производителями провести исследования и тесты, подобрать оптимальный технологический маршрут и материалы.
[1] Materials for Advanced Packaging, edited by D. Lu and C.P. Wong, Springer, 2008
[2] http://blog.dowelectronicmaterials.com/en/posts/2016/12/copper-pillar-electroplating-tutorial
[3] Thick Resist Processing, URL: https://www.microchemicals.com/downloads/application_notes.html
[4] Technic Inc., TechniStrip NI 555 Product description
[5] A.C. Mackie, Spin-Coating Waferbumping Fluxes for Semiconductor Assembly: Ensuring Pristine Microbumps in Dimensional Devices, Indium Corporation Tech Paper, 2013
Статья опубликована в журнале «Вектор высоких технологий».
Бесплатная подписка на журнал: https://ostec-group.ru/group-ostec/pressroom/journal/podpiska/
Официальный сайт Группы компаний Остек: https://ostec-group.ru/
Понравилась статья? Поставьте лайк