Здесь мы собираем самые интересные статьи, интервью, репортажи и многое другое. Зарегистрируйте личный кабинет и вам будет открыт полный доступ
Корпусирование МЭМС: проблемы и решения
Бойко, А., Гаев, Д., Тимошенков С.
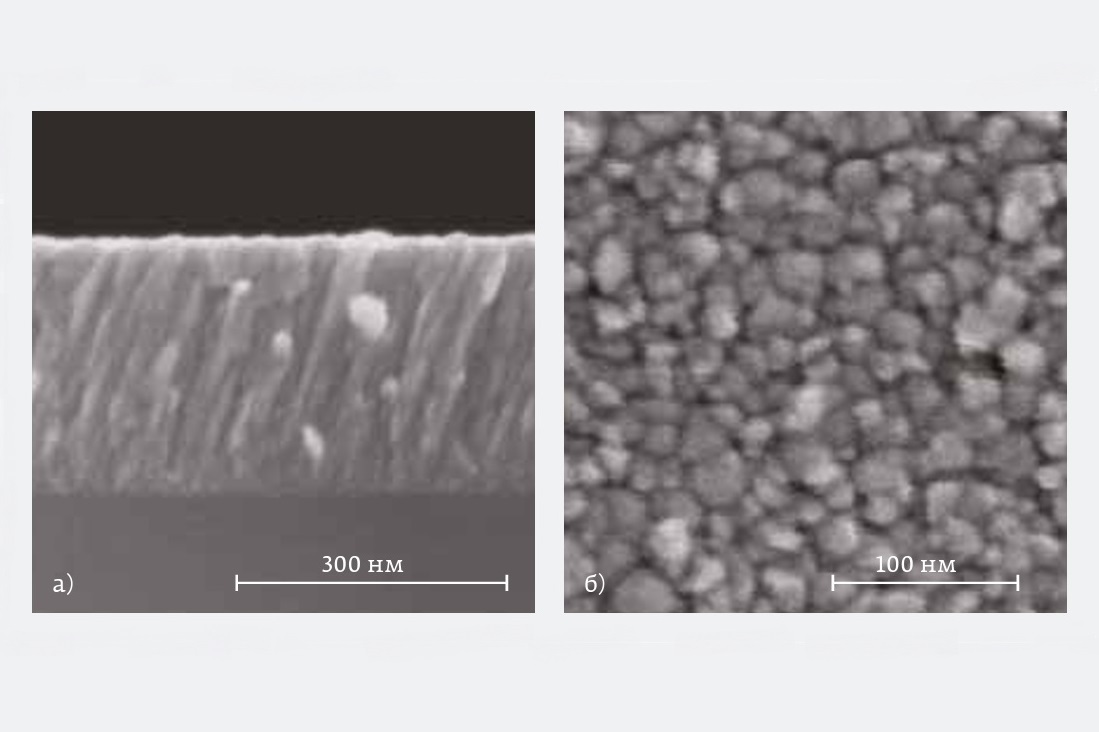
Конструктивные требования к изделиям микросистемной техники непрерывно повышаются: микросистемы становятся все более «интеллектуальными» и многофункциональными, при этом сохраняется тенденция к миниатюризации. Одним из наиболее сложных этапов производства микросистем является корпусирование, которое до сих пор остается «бутылочным горлышком» при решении задачи массового выпуска новых изделий. В настоящей работе сфокусировано внимание на проблемах, возникающих при разработке технологии корпусирования, и способах их решения.
Продолжающаяся цифровая революция основывается на интеллектуализации технических систем, в том числе на расширении возможностей их взаимодействия с внешней средой. Устройства нано- и микросистемной техники (НМСТ) продолжают быть основой индустрии Интернета вещей, робототехники, беспилотных транспортных средств. Востребованность нано- и микросистем сохраняется и будет только увеличиваться в обозримом будущем, что привлекает в эту отрасль новых игроков. Однако начинающие разработчики сталкиваются с рядом барьеров, первый из которых связан с усложнением конструкционных требований, а второй обусловлен сложностью технологических задач корпусирования микросистем [1].
УСЛОЖНЕНИЕ НАНО- И МИКРОСИСТЕМ
История микросистемной техники как отдельного технологического направления насчитывает более 50 лет. За точку отсчета можно взять создание в 1965 году полевого транзистора Натансона с трехмерным резонансным затвором [2]. Устройство, предназначавшееся для высокодобротной частотной селекции в кремниевых интегральных схемах, было создано на базовых принципах микросистемной техники: наличие трехмерных компонентов, групповая обработка, совместимость с технологиями кремниевых интегральных схем.
Рис. 1. Эволюция промышленно выпускаемых МЭМС-устройств
Эволюция МЭМС-устройств продолжается. От конструкций типа «одно устройство – одна функция» происходит переход к сложным комбинированным устройствам, объединяющим в единой конструкции преобразовательные и исполнительные элементы разных типов, а также микропроцессоры. В микросистемах, в особенности для Интернета вещей, начинают применять искусственный интеллект и машинное обучение [3]. Схематично эволюция выпускаемых промышленно МЭМСустройств изображена на рис. 1 [3]. Тренд к усложнению выполняемых функций (комплексирование) при одновременном повышении производительности и точности устройств приводит к необходимости увеличения затрат на разработку новых изделий.
КОРПУСИРОВАНИЕ КАК ТЕХНОЛОГИЧЕСКИЙ БАРЬЕР
Корпусирование до сих пор остается сложным технологическим барьером, особенно при решении задачи массового выпуска новых изделий НМСТ, что объясняется рядом причин. Во-первых, в индустрии НМСТ до сих пор не созданы единые стандарты в области корпусирования, сборки и монтажа ввиду конструктивного разнообразия микросистем. Во-вторых, большинство МЭМС содержат подвижные компоненты, для функционирования которых необходимо предусматривать вакуум-плотное корпусирование и обеспечивать свободное внутреннее пространство. И наконец, для ряда высокодобротных конструкций датчиков требуется создавать и поддерживать вакуум внутри корпуса.
Хотя единые стандарты по корпусированию отсутствуют, некоторые конструктивно- технологических решения уже доказали на практике свою эффективность и могут рассматриваться при разработке технологий корпусирования. В частности, перед разработчиками может стоять выбор между герметизацией микромеханических компонентов в индивидуальных корпусах и интегральным капсулированием типа «пластина к пластине». Для индивидуального корпусирования используются металлостеклянные или металлокерамические корпуса. Способ относительно прост и эффективен на стадии разработки изделий, так как позволяет использовать уже разработанные конструкции корпусов и отработанные технологические схемы. Однако в долгосрочной перспективе применение индивидуального корпусирования является, скорее, тупиковым решением из-за больших габаритов изделий и низкой производительности процессов герметизации, сборки и монтажа.
Рис. 2. Интегрально корпусированный микромеханический компонент с TSV-выводами
Интегральное корпусирование типа «пластина к пластине» уже является современной нормой в этой области и позволяет существенно уменьшить габариты микросистем. Помимо этого, капсулированные таким образом МЭМС-компоненты могут быть встроены в устройства более высокого уровня интеграции с применением современных технологий: 2,5D- и 3D-сборок, интерпозеров, сквозных межсоединений в подложке (TSV) и других. На рис. 2 схематично представлен микромеханический компонент, корпусированный с применением интегральных технологий.
Разрабатывая технологию корпусирования, можно выбирать способ соединения пластин и компонентов МЭМС. При использовании кремния и стекла как основных конструкционных материалов возможно применение различных технологических приемов: прямого соединения, соединения через промежуточный слой, анодного соединения. Характерные особенности технологий представлены в табл. 1.
Таблица 1. Особенности процессов соединения материалов, используемых в технологии герметизации микросистем
ВАКУУМ-ПЛОТНАЯ ГЕРМЕТИЗАЦИЯ И ВАКУУМИРОВАНИЕ
Уже на начальных этапах проектирования МЭМС необходимо определиться с выбором между вакуум-плотной и вакуумной герметизацией. Вакуум-плотным, согласно требованиям к корпусам микросборок [4], считается корпус, натекание в который не превышает 5 · 10–5 л · мкм рт. ст. / с. Данный уровень натекания обеспечивает незначительный газообмен между внутрикорпусной газовой средой и внешней атмосферой. Однако при необходимости вакуума внутри корпуса данный уровень натекания уже неприемлем, так как давление в корпусе МЭМС за короткое время возрастет на несколько порядков.
Герметизацию, обеспечивающую создание и сохранение вакуума во внутрикорпусном объеме, будем называть вакуумной герметизацией, или вакуумированием. Проведение такой герметизации микроприборов весьма затратно, так как требует тщательного выбора материалов корпуса и микроструктур, подбора соединительных материалов, а также высокого качества их подготовки и особых режимов проведения герметизации. Кроме того, может понадобиться использование газопоглотителей (геттеров) для создания и поддержания вакуума. Естественно, в данном случае речь не идет о газовых сенсорах и других датчиках, которым необходим контакт с внешней средой. Для подвижных механических структур, например акселерометров, гироскопов, микрофонов, ВЧ-переключателей, может потребоваться именно вакуумирование. Оно уменьшает рассеяние колебательной механической энергии в газовой среде, также называемое демпфированием сжатыми газовыми пленками (рис. 3). Соответственно, при вакуумировании увеличивается добротность резонансных механических структур, что важно для многих приложений. Помимо этого, уменьшается содержание влаги в корпусе, что снижает вероятность коррозии материалов, а также негативного эффекта «залипания» миниатюрных компонентов [5].
Рис. 3. Схематическое изображение капсулированного объема с геттером
На этапе разработки необходима оценка влияния остаточного давления на параметры преобразователя микромеханической системы. Для этого используются программные пакеты конечно- элементного моделирования МЭМС-компонентов. На рис. 4 представлена зависимость добротности от давления, построенная с использованием программного пакета ANSYS [6]. В качестве основных исходных данных при моделировании использовались размеры компонента, величина зазора между подвижной структурой и неподвижным основанием, вязкость газа и коэффициент аккомодации поверхности (учитывает взаимодействие молекул газа с поверхностью). В нашем случае размер подвижного компонента составлял 5,2 × 5 мм, зазор – 10 мкм. Результаты моделирования показали удовлетворительную корреляцию с данными, полученными при исследовании характеристик реальных структур. Следует отметить, что подобные модели являются упрощенными. В них не учитывается, например, мода колебаний. Поэтому результаты конечно- элементного анализа являются приближенными. Тем не менее, предварительные расчеты позволяют оценить диапазон значений давления, оптимальных для работы устройства.
Рис. 4. Зависимость добротности Q микромеханического компонента от давления р в полулогарифмическом масштабе
Отдельной задачей является контроль герметичности и остаточного давления в вакуумированных микроприборах. Способы оценки герметичности, применяемые в электронной промышленности, например метод опрессовки, обладают в данном случае недостаточной чувствительностью и могут применяться только для контроля технологического процесса и нахождения грубых течей. Поэтому необходимо выполнять предварительную калибровку микромеханических компонентов и проводить на этапе создания опытных образцов экспериментальные исследования зависимости параметров от давления. Это, во-первых, дает возможность скорректировать требования к рабочему внутрикорпусному давлению, а во-вторых, позволяет определять давление в устройстве после его корпусирования.
ПРИМЕНЕНИЕ ГАЗОПОГЛОТИТЕЛЕЙ ДЛЯ СОЗДАНИЯ И ПОДДЕРЖАНИЯ ВАКУУМА
Для получения в капсулированном объеме среды с пониженным давлением необходимо проводить герметизацию в условиях вакуума и обеспечивать предварительный нагрев компонентов для удаления остаточных газов с поверхности и объема конструкционных деталей (операция дегазации). Однако выполнение этих условий в технологии микросистемной техники не обеспечивает получения в корпусе среднего и тем более высокого вакуума, а также его поддержания в течение длительного времени. Компоненты микроэлектромеханических систем чаще всего не выдерживают длительного нагрева до температуры выше 300–400 °C, при которой вероятно возникновение термомеханических напряжений. Из-за этого возможности температурной активации в случае микромеханики ограничены. Помимо этого, газы, растворенные в конструкционных материалах, будут диффундировать к поверхности и попадать затем во внутренний объем, что приведет к деградации вакуума. Поэтому для поддержания вакуума в микросистемах используют, как и в случае электровакуумных приборов, газопоглощающие материалы (геттеры).
В микросистемной технике хорошо зарекомендовали себя геттерные пленки на основе Ti, Zr, V, Fe и других материалов, формируемые магнетронным или катодным распылением. Пленочные геттеры толщиной несколько микрометров могут быть относительно легко встроены в микромеханические приборы, в том числе с применением интегральных технологий типа «пластина к пластине» [7]. Активирование пленочных геттеров, то есть приведение их в рабочее состояние, может быть совмещено с основными способами соединения конструкционных материалов (табл. 1). Геттеры, изготавливаемые по порошковой технологии, как и распыляемые геттеры, неприменимы в МЭМС из-за больших габаритов и сложности встраивания в корпус.
Рис. 5. Изображения пленок Ti1-x Vx на кремниевой подложке, полученные сканирующей электронной микроскопией [9]: а – торец; б – поверхность
Основные материалы, используемые для создания газопоглотителей, – это Ti, V и Zr. Применяемые индивидуально или в составе многокомпонентных пленок, они позволяют создавать материалы с температурой активирования от 180 °C [8]. В своих работах мы использовали геттерные пленки Ti70 V30 (ат. %), формируемые методом магнетронного распыления [9]. Данный состав характеризуется относительно низкой температурой активации, от 300 °C, и высоким значением сорбционной емкости. Пленки обладают наноразмерной структурой с размером зерен от нескольких единиц до десятков нанометров (рис. 5а и б).
Наноструктурирование способствует увеличению поверхности межзеренных границ, что, в свою очередь, увеличивает скорость сорбции и удельную сорбционную емкость геттеров. Управление структурой геттерных пленок в случае магнетронного распыления возможно путем варьирования технологическими режимами (температурой подложки, давлением рабочего газа, скоростью напыления), а также углом наклона подложки относительно мишени.
А. Бойко, к. т. н.1, Д. Гаев, к. х. н.2, С. Тимошенков, д. т. н.3
Статья впервые опубликована в журнале "ЭЛЕКТРОНИКА: НТБ" № 2 за 2022 год.
___________________________________________________________________________________________________
ЛИТЕРАТУРА
- Бородина И., Бойко А., Мильшина Ю., Вишневский К., Киселева Л., Пучков В. Микро- и наносистемы становятся все меньше и все «умнее» // Глобальные технологические тренды. Информационный бюллетень, № 9, М.: НИУ ВШЭ, 2017. https://issek.hse.ru/trendletter/news/208033243.html.
- Nathanson H. C. at al. The resonant gate transistor // IEEE Transactions on Electron Devices, vol.14, no.3, pp. 117–133, Mar 1967, DOI: 10.1109/T-ED.1967.15912.
- The MEMS success story: a decade of evolving strategies leading to a bright MEMS future – An interview with Bosch Sensortec, STMicroelectronics and Yole Développement, https://www.imicronews.com/the-mems-success-story-a-decade-of-evolvingstrategies-leading-to-a-bright-mems-future-an-interview-withbosch-sensortec-stmicroelectronics-and-yole-developpement/.
- Корпуса микросборок. Технические условия ПИЖМ.430114.001.
- Тимошенков С. П., Бойко А. Н., Симонов Б. М., Заводян А. В. Технологии вакуумной герметизации МЭМС //Известия вузов. Электроника, № 1, 2010. С. 11–24.
- www.ansys.com.
- Скупов А. Вакуумное корпусирование на уровне пластины – геттеры // ЭлЕКТРОНИКА: Наука, Технология, Бизнес, № 5, 2016. С. 54–59.
- Benvenuti C., Chiggiato P., Costa Pinto P., Prodromides A., Ruzinov V. Influence of the Substrate Coating Temperature on the Vacuum Properties of Ti-Zr-V Non- Evaporable Getter Films // Vacuum, Vol. 71, Issues 1–2, 2003, pp. 307–315.
- Бойко А. Н., Калмыков Р. М., Гаев Д. С., Сырчин В. К., Тимошенков С. П. Нераспыляемые геттерные структуры для МЭМС // НАНОИНДУСТРИЯ. Спецвыпуск (74). 2017. C. 561–565.
Понравилась статья? Поставьте лайк