Здесь мы собираем самые интересные статьи, интервью, репортажи и многое другое.
Совершенствование процесса пайки волной припоя с модернизированной системой подачи азота
Ольга Жиляева, ООО «ЭР ЛИКИД», M. Theriault, P. Wolff, Air Liquide GmbH, R. Passman, K. Redwitz, Siemens AG
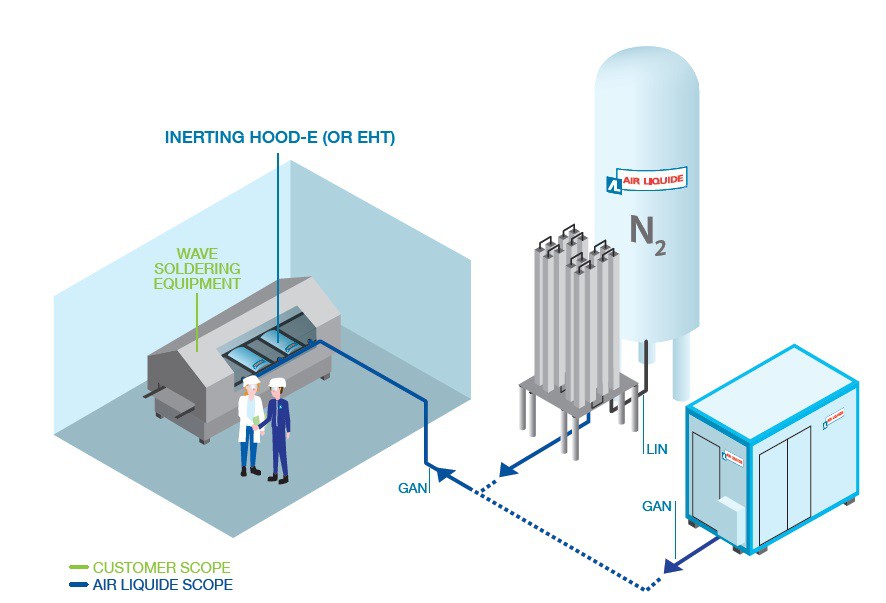
Несмотря на предсказания скорой кончины процесса волновой пайки, эта технология монтажа радиоэлементов продолжает широко использоваться на производстве. В статье описывается применение простой модернизированной системы волновой пайки с использованием азота на предприятии, занимающемся смешанным монтажом радиоэлементов при производстве оборудования для связи и другой продукции. Обсуждаются факторы, стимулирующие переход процесса сборки печатных плат с использованием инновационных систем впрыска азота, и целесообразность такого перехода. Представлен обзор и анализ технических результатов и затрат, а также преимуществ данной модернизации.
Введение
При определении направления дальнейшего развития технологий пайки, часто высказывается мнение об ограничении возможностей для использования процесса пайки волной припоя, и, тем не менее, этот метод все еще продолжает находить свои области применения. Новые технологии сборки в объемном корпусе развиваются в направлении использования более мощных устройств меньших размеров, однако, по-прежнему существует спрос на пайку компонентов и изделий, монтируемых в отверстия на плоских монтажных платах (SMT). Механическая прочность, необходимая для соединений, а также более низкие затраты на пайку волной припоя способствуют широкому распространению данного способа. Среди инноваций в процессе волновой пайки можно отметить спрей-флюсование, конвекционный предварительный нагрев в сочетании с использованием азота в качестве инертной атмосферы. Процесс волновой пайки в азоте не нов, но в последнее время он значительно изменился. Сегодня имеются новые, простые и оптимизированные решения подачи инертного газа в зону пайки, которые упрощают переход от пайки в воздушной атмосфере к инертной (азотной).
Применение азотной атмосферы в промышленных системах увеличивается как в новых, так и в модернизированных системах пайки. За счет уменьшения окисления и увеличения поверхностного натяжения образуются более сильные адгезионные связи и более быстрое смачивание контактных поверхностей. В результате повышается качество пайки и сокращается количества дефектов. Улучшается и прочность паяных соединений, что обеспечивает более высокую надежность. Уменьшается образование шлака, что дает экономию припоя, а также благоприятно для окружающей среды, здоровья и производства.
Несмотря на привлекательность в целом, многие потенциальные пользователи еще не оценили должным образом пайку волной припоя в инертной среде. Одна из причин – значительные капиталовложения, необходимые для модернизации печей с целью внедрения данной методики. Кроме того, еще несколько лет назад соотношение цены качества в области применения азота в процессе пайки волной припоя оставалось все еще неясным и не служило обоснованием для дополнительных капитальных затрат на такое оборудование.
Жизнеспособность волновой пайки и специфические потребности в технологии инертной среды привели к разработке нового способа использования инертной атмосферы. В результате появились простые и эффективные решения, как для нового оборудования, так и для модернизации существующего. Так как общие затраты на пайку в инертной среде с помощью новых устройств становится намного ниже, то производитель может оценить, улучшится ли качество и сократятся ли расходы на процесс волновой пайки.
Преимущества модернизированного процесса пайки в среде азота
Внедрение новой системы подачи газа для процесса пайки в инертной атмосфере было проведено на заводе, где выпускается телекоммуникационная продукция. Завод оснащен многочисленными линиями монтажа компонентов на поверхность монтажной платы (SMT). Кроме того, имеются две машины для пайки волной припоя: туннельная машина с закрытой инертной атмосферой и обычная машина для пайки волной припоя, требующая постоянной подачи азота в большом объеме. Изготовителем последней является Streckfuss, поставщик оборудования для пайки из Германии. Численность персонала предприятия превышает 1600 человек. Завод работает в три смены при 5-дневной рабочей неделе.
Данному предприятию была предложена новая, инновационная система подачи азота, протестировать которую решили на машине Streckfuss. Цель заключалась во внедрении этой системы в производство, если ее преимущества смогут обеспечить более короткий период выхода на рынок изделий и снижение производственных затрат.
В ходе тестирования нужно было определить следующее. Во-первых, насколько можно увеличить межсервисный интервал работы линии сборки. Вследствие образования шлака машина требовала частой очистки и обслуживания, что приводило к значительным затратам (около 2-3 час ежедневно). Во-вторых, снизить потери, связанные с образованием шлака, а также в результате перехода на пайку в инертной атмосфере получить возможность открыть «технологическое окно» для процесса с низким количеством твердых примесей, не требующего очистки. В-третьих, повысить надежность сборки.
Новая модернизированная азотная технология
Предлагаемая модернизированная система – это один из способов формирования инертной «завесы» (blanket-type), внедренный некоторое время назад. Преимущества данного метода организации инертной среды при пайке волной припоя в сравнении с другими подробно описаны многими специалистами [2]. Технологии формирования инертной завесы для ванны с припоем создается посредством удержания газообразного азота на границе печатной платы и волны припоя. Когда волны припоя достигают печатной платы, азот полностью покрывает их, концентрируясь в пространстве между платой и припоем. За долю секунды в атмосфере в нижней части платы содержание кислорода становится менее 10 ppm, что сопоставимо с исходным качеством азота. Эта система работает в открытом пространстве, для нее не нужно какого-либо ограждения или завесы, чтобы поддерживать инертную среду.
Подобно другим азотным системам, принятая в эксплуатацию новая система подачи азота состоит из панели газораспределения, устройства впрыска и соединяющего их гибкого трубопровода. Газовая панель регулирует поступление азота из установки и направляет его к устройству впрыска. Однако представленная система значительно отличается от других систем создания инертной среды с образованием защитного слоя. Решение, предназначенное для подачи азота, состоит из трех пористых распылителей, заключенных в титановую раму - камеру повышенного давления (ресивер). Ресиверы соединены между собой и превращают систему в единую сборную конструкцию (рисунок 1), служащую для нескольких целей и содержащую распылители, направляя ламинарный поток азота над поверхностью волны припоя и поддерживая всю систему в положении, предотвращающем проникновение воздуха со стороны тигля. В каждом ресивере имеются отверстия специальной формы, что позволяет поддерживать равномерное, дозированное поступление инертной атмосферы к волне припоя. Этот метод обеспечивает необходимую скорость и оптимизирует процесс подачи защитного газа. Кроме того, он предотвращает засорение (забивание) азотных распылителей парами флюса. В зоны крутого наклона волн, критические с точки зрения образования шлака, благодаря барботированию расплавленного припоя постоянно поступает инертный газ и за счет этого образование шлака сильно уменьшается. Вся конструкция находится между форсунками волны припоя (рисунок 2).
Основной особенностью новой технологии является метод подачи газа. Небольшое повышение давления азота и его направленная диффузия через отверстия в ресивере позволяют размещать данную конструкцию в систему волновой пайки любого типа. Поэтому установка не требует каких-либо изменений форсунок или иных модификаций системы формирования волны припоя. Такая особенность позволяет пользователю оборудовать или модернизировать установку фактически любой марки и модели для пайки волной припоя.
Рис. 1. Приспособление для подачи азота
Рис 2. Принцип действия новой системы подачи
Применение
Конструкции оборудования для волновой пайки различных производителей значительно отличаются друг от друга. Ванны с припоем и конфигурация форсунок одного и того же производителя так же часто имеют свои особенности, в зависимости от модели. Отсюда следует, что система впрыска азота должна быть приспособлена к любому выбранному оборудованию. Благодаря этому каждый распылитель оптимизируется и адаптируется к работе определенной машины.
После предварительного анализа конструкции ванны с припоем была организована серия измерений. Они позволили получить точные данные о размерах ванны с припоем и форсунок припоя, на основании которых можно было подготовить чертежи для азотной системы и спроектировать установку. После остановки машины ванна с припоем была снята, обе форсунки были демонтированы и очищены. Были измерены и угол конвейера, и высота волны. Определено будущее расположение газовой системы. Особенность данной установки состояла в том, что она оснащена обычной турбулентной и ламинарной волной, а форсунки были расположены под углом 70° по ходу конвейера, что связано с необходимостью уменьшения образования перемычек припоя между контактами. После очистки тигля и всего блока форсунки были снова установлены, и машина запущена в эксплуатацию. Весь процесс занял 2 ч и был проведен в период снижения темпов производства.
Настройки процесса и условия эксплуатации
Все параметры волновой машины с азотной системой подачи были проверены перед сдачей в эксплуатацию. Такие характеристики, как высота волны и количество флюса, зависящие от качества азотной атмосферы, контролировались очень тщательно. Платы имели различные размеры, обычно FR-4 с дополнительным покрытием HASL или Ni/Au, односторонние или двусторонние. Так же еще использовалось органическое защитное покрытие (OSP). Материал припоя - Sn63Pb37 с низким уровнем образования шлака.
Выбор флюса
Выбор флюса оказывает непосредственное влияние на спаиваемость, а также на достигаемую в результате чистоту сборки после пайки. В качестве инновационной меры по улучшению процесса за год до начала инертизации был осуществлен переход на безотмывочный флюс. Пенный флюсователь был заменен спрей-флюсователем, и содержание твердых примесей в среде флюса изменилось с 20% до 2%. Преимущества проявились сразу же: увеличились значения сопротивления изоляции поверхности (SIR), флюс и спирт использовались более экономно, сократились операции по перемещению и хранению спирта, в значительной степени снизились выбросы летучих органических соединений (VOC). Однако эти изменения способствовали и сужению «технологического окна». Поддерживать требуемое количество дефектов на миллион возможностей (dpm) на приемлемом уровне стало сложнее, и для каждой новой партии плат и компонентов следовало выполнять точную настройку. Переход на азот рассматривался как мера для повторного открытия этого «окна». Было точно установлено, что применение азота позволяет использование более мягких флюсов (или меньшего количества флюса), чем это могло бы быть допустимо в атмосфере воздуха для данного производителя.
Уровень кислорода и потребление азота
Для системы пайки с газовой защитой волны припоя контроль примесей кислорода (в ppm) является коренным отличием по сравнению с обычными системами.
Печатная плата является неотъемлемой принадлежностью метода пайки с использованием инертной среды, так как она играет роль крыши (изоляции) над волнами припоя. Когда печатная плата входит в волну, пространство под печатной платой моментально продувается азотом, впрыскиваемым распылителями. Теоретические расчеты позволяют сделать оценку и показать, что пространство между волной, распылителем, ванной с припоем и печатной платой за одну секунду обновляется 10 раз. Поэтому на границе раздела плата / волна может быть обеспечена атмосфера с низким содержанием кислорода. Однако, когда нет платы, которую нужно паять, отсутствует эффект «крыши» и защитная атмосфера становится не такой чистой. Вот почему измерения уровня кислорода в значительной степени отличаются в зависимости от того, имеется ли плата в зоне пайки или ее нет.
Была выполнена проверка уровня кислорода в ppm с помощью газоанализатора кислорода, оснащенного циркониевой камерой. Системы с циркониевой камерой имеют высокую скорость реакции, необходимую для часто чередующихся измерений. Рассматривались две схемы настройки;
-
Имитация платы с просверленными отверстиями и подсоединенными измерительными трубками;
-
Вставка измерительной трубки из нержавеющей стали между волной и распылителями, вблизи печатной платы, расположенной в центре системы впрыска N2.
Последний метод был избран потому, что он дает правильное измерение с платой или без нее (Рисунок 3). Этот метод мог бы использоваться постоянно и обеспечивать контроль уровня кислорода как способ контроля качества.
Рис. 3. Схема измерения содержания примесей кислорода
Расход азота для каждого распылителя был установлен на основании опыта использования других подобных процессов, точно отрегулированных для обеспечения наилучшего соотношения O2 ppm/ N2. Обширные исследования и тесты показывают, что все преимущества систем пайки волной припоя в инертной среде могут быть достигнуты только в атмосфере азота с содержанием кислорода не более 50 ppm [3]. Для сравнения азот, вырабатываемый криогенным способом, содержит обычно максимально 3 ppm O2. В таблице приведены результаты теста.
Таблица 1. Потребление азота и содержание примесей кислорода в ppm.
Важно отметить, что величина расхода азота – это данные о мгновенном расходе, а не фактический общий расход газа. Применение электромагнитного клапана с системой включения насоса сокращает общий расход газа, приводя, таким образом, к экономии азота. Кроме того, когда не используется турбулентная волна, распылитель номер 1 отключают. Нетрудно предположить, что приведенные выше величины расхода азота могут быть ниже для форсунок меньших размеров, где имеется меньшая потребность в инертной среде.
Результаты и технические преимущества
После шести месяцев работы и тысяч паяных плат было установлено, что переход от воздушной атмосферы к новой системе пайки волной в инертном газе превзошли первоначальные ожидания. Соответственно, система была принята для постоянного применения.
Образование шлака
Наиболее важным преимуществом употребления азота в процессах пайки волной припоя является уменьшение образования шлака. Шлак - это серебристый шлам, покрывающий поверхность ванны с припоем. Он состоит, главным образом, из нормального припоя и определенного количества окиси олова, возможно присутствие определенного количества двуокиси свинца. Шлак образуется, когда расплавленный припой на поверхности ванны контактирует с кислородом. Тонкая пленка шлака имеет и свои преимущества, поскольку защищает ванну от окисления, но его большое накопление неблагоприятно для процесса в целом. Естественно, что использование инертной атмосферы в значительной степени ограничивает образование шлака.
После более чем 3 000 часов эксплуатации скорость образования шлака при использовании инновационной системы впрыска азота была на среднем уровне 0,3 кг/ час. Иногда это значение меняется вместе с производственной нагрузкой, шириной паяемой платы и в зависимости от того, применяется или нет турбулентная волна. Значительное влияние оказывает периодичность и длительность остановки волны (технологические паузы). Указанное выше значение – это вес шлака, собранного в результате процесса очистки. При этом реагент «для предотвращения образования шлака» не использовался. Если сравнить полученный результат со значениями, характерными для процесса пайки в воздухе, при тех же, условиях (2,08 кг/ час), мы приходим к выводу, что образование шлака снизилось на 85%.
Техническое обслуживание и время безотказной работы оборудования
Техническое обслуживание ванны с припоем может занимать много времени. Для обеспечения надлежащей работы насосов и хороших параметров волн и, следовательно, результатов процесса пайки, шлак необходимо удалять довольно часто. А когда производство работает в три смены, то техническое обслуживание заметно сокращает эффективное время работы сборочной линии. Уменьшение образования шлака приводит к снижению потребностей в необходимом обслуживании и позволяет повысить уровень производительности. Если до введения азота обслуживание выполнялось 4-5 раз в день (2,0 – 2,5 часа / день), теперь оно было сокращено до 30-минутной процедуры один раз в день. Это ежедневно дает дополнительные два часа производственного времени в день. Кроме того, уменьшение времени, нужного для очистки машины, обеспечило более высокую гибкость в оптимизации производственного процесса. Теперь операторы могли выполнять необходимую операцию во время плановой остановки производства, отпала необходимость в срочном контроле и немедленной очистки, когда проблемы становились видимыми.
Что касается азотной системы, ее использование над форсунками припоя не вызвало каких-либо проблем с обслуживанием. Ее можно быстро снимать и снова устанавливать, когда следовало выполнить чистку ванны с припоем. Сама система не требовала какого-либо ухода или запасных частей даже через шесть месяцев работы.
Результаты по качеству и анализ дефектов
Как уже указывалось в многочисленных исследованиях и статьях [2,3], пайка в атмосфере азота изменяет два критических параметра, оказывающих влияние на качество пайки волной припоя:
-
Азот уменьшает окисление, что снижает образование шлака, потребность в обслуживании ванны с припоем;
-
Азот повышает поверхностное натяжение на волне расплавленного припоя и увеличивает смачивание поверхности контактов.
Поскольку шлак может привести к возникновению дефектов пайки, а смачивающая способность является индикатором качества и геометрии соединений, то предполагалось, что азот может улучшить качество паянного соединения. Относительно этого вопроса все сходятся во мнении, что при пайке в среде азота происходит увеличение “окна возможностей” для производства. Пайка в среде азота становится менее требовательной, чем в среде воздуха. «Окно возможностей» могло бы быть еще увеличено, но нужно ли это и оказывает ли это влияние на уровень надежности и дефектности?
На рисунке 4 показан процесс пайки волной припоя (число дефектов на 1 миллион возможностей (dpm)) до и после перехода на азот для «проблемной платы». Общий уровень дефектов при таком устройстве сборки печатных плат низкий - менее чем 10 dpm. Так как для проверки улучшений на этом уровне необходимы образцы особенно больших размеров, то для демонстрации эффективности новой технологии пайки в инертной среде был выбран специальный сборочный узел с несколькими проблемными выводами. Данные выборки для замера уровня дефектности ‘до’ и ‘после’ для этой платы сделаны с периодом в шесть месяцев. Количество дефектов (dpm) отражает количество соединений, не проходящих контроль (для соединений, пайка которых происходит только волной припоя). Специалисты в области контроля, испытаний и исправления дефектов сообщают о каждом отдельном дефекте. Этот метод регистрации представляет собой контроль показателей производственного процесса и помогает отслеживать качество процесса.
Рис. 4. Анализ дефектов: до и после введения азота (период в шесть месяцев для «проблемной платы»)
С введением азота количество дефектов (dpm) для данного конкретного узла уменьшилось со 150 до уровня 60 – 70 dpm. Общее снижение показателя составило 55% – 60 %. Для этого изделия сократилось количество дефектов всех типов. Таким образом, можно говорить об общих преимуществах, которые должны проявиться и в других изделиях и способны привести к дальнейшему снижению уже и сейчас низкого числа дефектов (dpm). Повышение поверхностного натяжения, связанное с использованием азота, не выразилось в заметном образовании перемычек припоя, относительно чего ранее высказывались опасения. Формирование перемычек на контрольных образцах значительно сократилось, что снижало частоту случаев исправления дефектов. Поскольку возникновение перемычек во время пайки двойной волной происходит в выходной зоне второй волны, это благоприятно и для процесса смывки (удаления) флюса. Подобное явление объяснение тем, что при пайке в атмосфере азота обеспечивается более высокая активность флюсования для выходной зоны.
Предполагается, что уменьшение числа дефектов, связанное со смачиванием, должно происходить в том же самом направлении. При температурах, достигаемых в волне, использование азота – это эффективный путь предотвращения окисления металлических поверхностей на плате, которые должны быть соединены пайкой. Отсюда активность флюса не истощается из-за взаимодействия с окислами металлов, которые могут образоваться в воздухе при нагреве. Более тонкий слой окислов требует меньшую активность флюса, поэтому он может более интенсивно влиять на смачивание и снижать поверхностное натяжение в области выхода волны.
Хотя азот способен косвенно влиять на образование шариков припоя при пайке волной припоя, этот фактор здесь не наблюдался. Считается, что качество паяльной маски и флюс сопоставимы с пайкой волной в среде инертного газа. Объяснение этого явления и предлагаемые решения детально описаны в статье. [4].
Наибольшие преимущества отмечены при тестировании плат с матричными контактными полями (подпружиненные контакты). Количество ошибок при испытаниях иглой значительно уменьшилось. Сократилось и число случаев вмешательства человека. Более низкое содержание твердых частиц в сочетании со снижением скорости осаждения (спрей-флюсование) – основные меры решения данной проблемы. Кроме того, некоторые флюсы при использовании азота обеспечивают дальнейшее улучшение процесса, поскольку в атмосфере инертного газа отсутствует окисление компонентов флюса. Общее влияние азота в сравнении с воздухом при проведении этих испытаний оценивается как положительное, но это не было задокументировано. Тем не менее отдельные исследования показывают [5], что азот уменьшает остатки некоторых флюсов в сравнении с их использованием в воздухе.
В целом и в данном конкретном случае, параметры качества при пайке волной припоя, выполненной с использованием новой системы подачи азотной завесы, сопоставимы с результатами пайки с помощью машины туннельного типа с полностью закрытой инертной системой.
Экономика процесса
Вдобавок к увеличению времени безостановочной работы азот и новая система впрыска азота снизили производственные затраты на линии. Сравнение расходов с экономическими преимуществами касается гораздо большего числа факторов, кроме стоимости азота. Основываясь на имеющихся результатах, данные о затратах и экономии выглядит следующим образом:
Стоимость системы модернизации и газа:
Общая сумма затрат: Система модернизации с азотом и стоимость N2 в час: $3,50/час
Достигнутая экономия:
Уменьшение количества шлака: $8,00/час
Уменьшение затрат на техобслуживание: $2,00/час
Чистая экономия (измеренная): $6,50/час
Другие виды экономии и преимущества:
- Гораздо более продолжительное время безотказного функционирования линии;
- Ремонт и сокращение операций по доработке находится в стадии изучения;
- Уменьшение расходных материалов (спрей, воздух в сравнении с азотом: 25% ( в будущем));
- Меньше загрязнений на плате;
- Положительное влияние на окружающую среду.
При более чем 6000 часов работы производства в год чистая экономия, достигаемая за счет перехода на азот с новым комплектом оборудования для модернизации линии, достигает $ 40 000 в год. Рассматривая расходы на всю линию пайки в 1 час для крупных современных монтажных установок, можно утверждать, что экономия оказывается намного больше, если к этому добавляется время безотказной работы и уменьшение необходимости в переделке. Эти данные относятся только к процессу пайки волной припоя.
Заключение
Модернизация существующего оборудования для пайки волной для применения азота происходит теперь проще и удобнее благодаря новым оптимизированным устройствам подачи инертного газа.
Выбор усовершенствованной системы подачи азота представляется оптимальным даже в при таких сложных условиях, как большой угол наклона форсунки в 70º. Процедура модернизации потребовала лишь минимального перерыва в напряженном производственном графике.
Использование инертной среды в критической зоне между ресивером для подачи азота и волнами припоя показало отличный результат. Количество дефектов припоя значительно уменьшилось. Качество используемого инертного газа обеспечило качество пайки, сопоставимое с результатами, полученными с помощью туннельной машиныс полностью закрытой инертной системой.
Уменьшение образования шлака вызвало общее уменьшение потребности в обслуживании. Сокращение времени на обслуживание выражалось в значительных преимуществах, проявляющихся увеличении производительности линии пайки; в пересчете на год сокращение потерь времени для производства составило около 500 часов.
Расчеты затрат показывают, что затраты на модернизацию и потребленный азот низки в сравнении с экономией и получением дополнительного времени для производства.
Литература
-
M. Theriault, P. Blostein; “Reducing the Cost of Inert Soldering” (Снижение затрат на пайку в инертной атмосфере); Circuit Assembly Magazine, July 1998, pages 46-52.
-
S. Duplan; “New Nitrogen Wave Soldering Concept” (Концепция нового процесса пайки волной припоя в азоте); Proceedings of Nepcon West 1994.
-
A. Rahn; “Nitrogen for Flow and Reflow Soldering?” (Азот для пайки волной припоя и пайки оплавлением припоя; SMTA Newsletter, Aug./Sept. 1997
-
B. Triennes, G. Kozick; “Eliminating Solder Balls in an Inert Wave Soldering Process” (Устранение шариков припоя при процессе пайки волной припоя в атмосфере азота) ; Proceedings of Nepcon West 1996.
-
Thibault, Bell, Lemieux; “Reduction of Residues Using Various Atmospheres” (Уменьшение остатков с использованием различных атмосфер); Proceedings of NEPCON West 1998.
Познакомьтесь с решениями компании ООО "Эр Ликид": https://industry-hunter.com/AirLiquide
Понравилась статья? Поставьте лайк
Электроника Производство электроники Монтаж штыревых компонентов (THT)
Читайте также
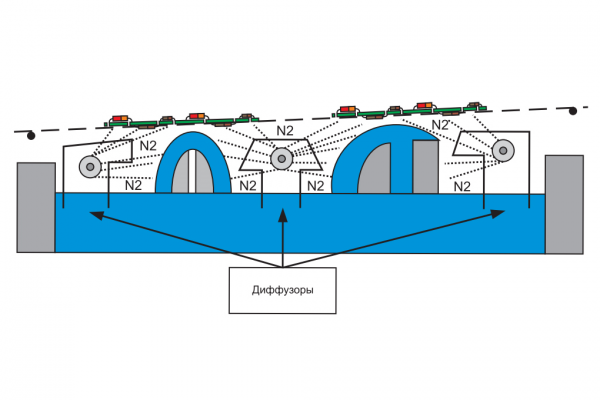
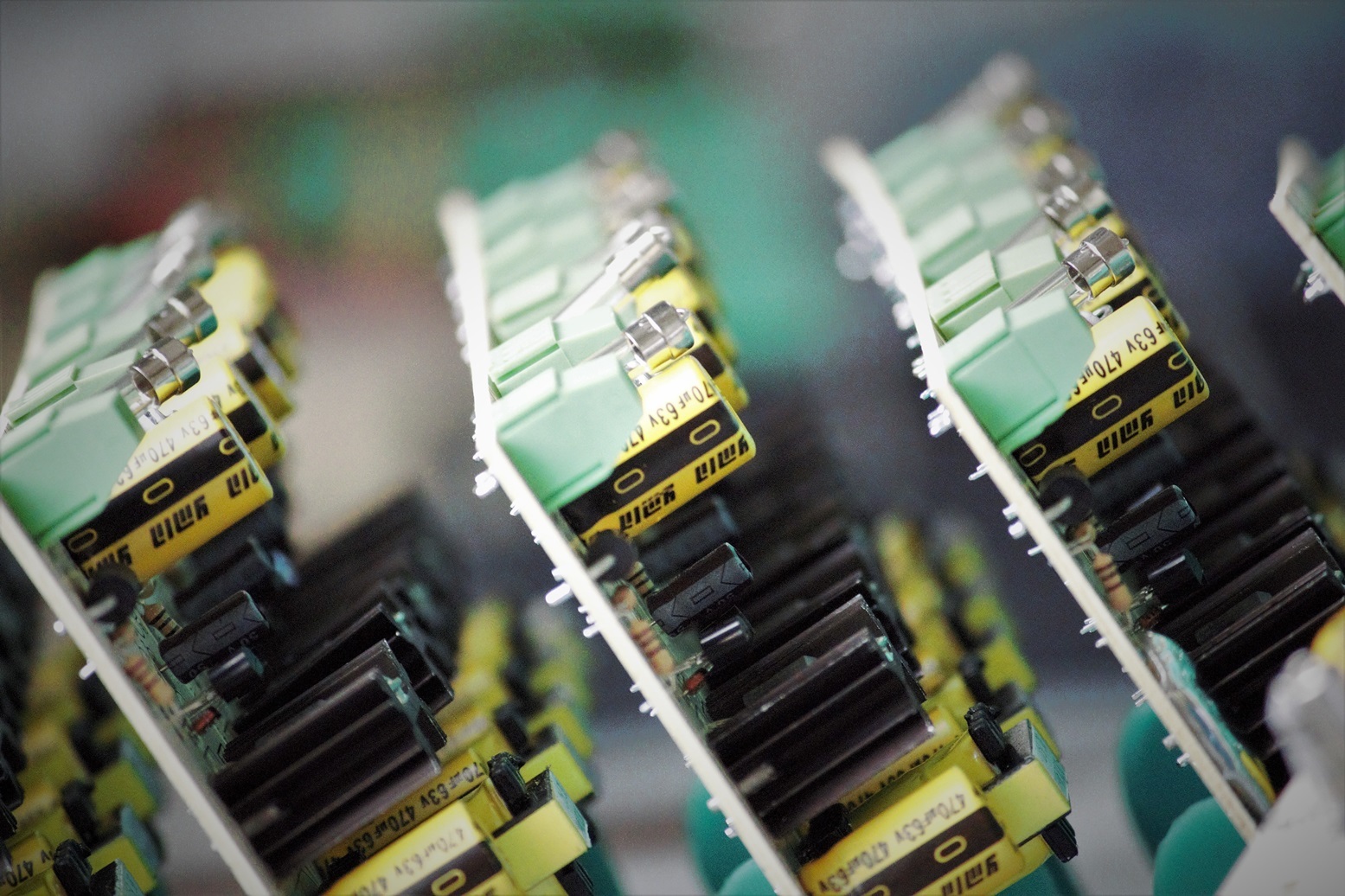
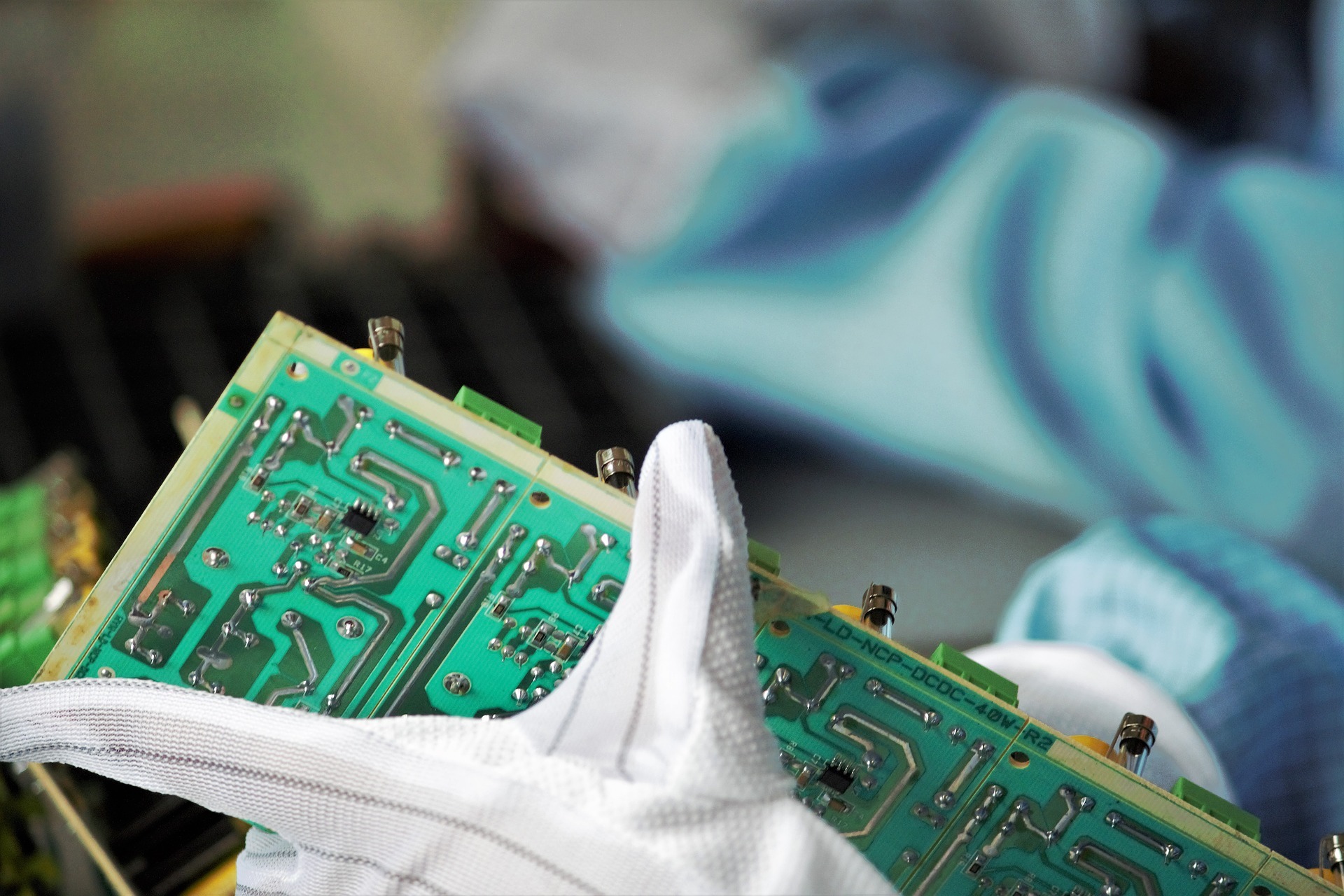