Здесь мы собираем самые интересные статьи, интервью, репортажи и многое другое.
Стойкость бессвинцовых сплавов к ударным (динамическим) нагрузкам. Эффект микродобавок
Ранджит С Пандер (Ranjit S Pandher), Брайен Г Левис (Brian G Lewis), Рагхасудха Вангавети (Raghasudha Vangaveti), Бава Сингх (Bawa Singh)
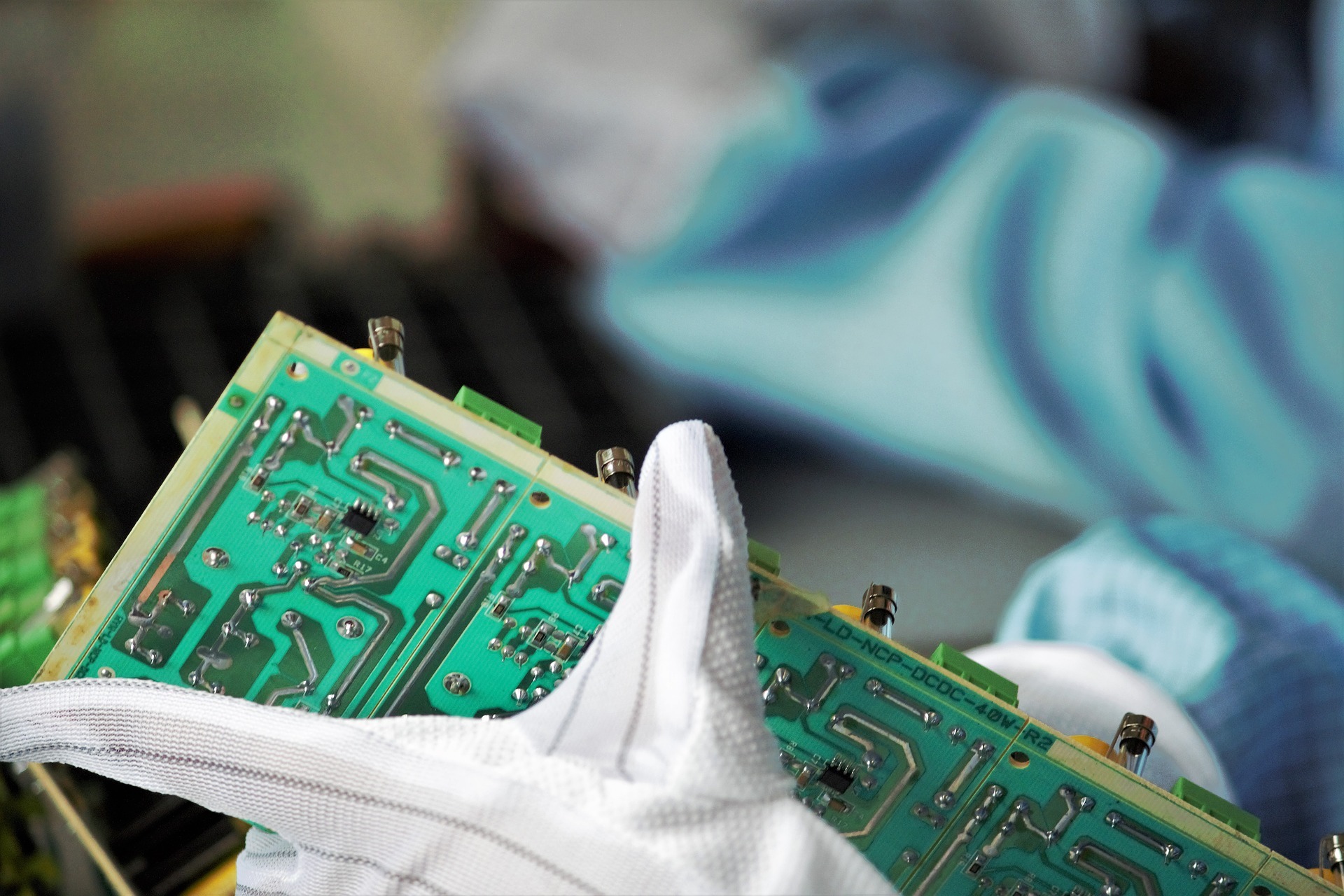
Статья предоставлена компанией «Itecs»
www.alphametals.ru
Впервые опубликовано в журнале «Технологии в электронной промышленности», №7/2012
Авторы: Ранджит С Пандер (Ranjit S Pandher), Брайен Г Левис (Brian G Lewis), Рагхасудха Вангавети (Raghasudha Vangaveti), Бава Сингх (Bawa Singh)
Перевод: Виталий Щекин, Алексей Максимов
info@alphametals.ru
Краткое описание
Вопрос надёжности паяных соединений является одной из основных тем в электронной промышленности частично из-за постоянно растущей популярности мобильных электронных устройств и частично ввиду перехода на бессвинцовые паяльные материалы. Большинство рекомендуемых бессвинцовых сплавов (Pb-free) – это сплавы с большим содержанием олова (high Sn) и относительно высоким показателем модуля упругости и прочности. Это и играет ключевую роль в вопросе надёжности бессвинцовых паяных соединений. Более того, несмотря на то, что именно олово в припойных сплавах принимает основное участие в образовании паяного соединения, интерметаллические соединения, образованные использованием оловянно-свинцовых (SnPb) и бессвинцовых сплавов (Pb-free), могут различаться. На качество паяного шва также влияет и очевидно различающиеся режимы процесса для оловянно-свинцовых и бессвинцовых сплавов.
Хрупкий излом паяных соединений при термоударах образуется вблизи или непосредственно в промежуточном слое (слоях) интерметаллических соединений. Это происходит из-за хрупких свойств интерметаллических соединений, дефектов как внутри, так и на границе интерфейсов, а также в результате передачи напряжений промежуточным слоям по причине низкой вязкости припоя.
В процессе работ по улучшению характеристик сплавов компанией Cookson Electronics учитывались два основных направления – это повышение вязкости припоя, а также модифицированный контроль интерметаллических слоев. Широкий диапазон основных составов сплавов вместе с отобранными микросплавными добавками к сплавам на основе SnAgCu оценивались с целью контроля механических свойств и процессов диффузии, действующих при образовании и росте промежуточных интерметаллических слоев.
В данной статье приведены результаты глубокого изучения ряда микросплавных добавок. Сплавы-добавки обычно действуют как модификаторы диффузного отражения молекул, снижая взаимную диффузию между подложками и припоем, а также уменьшая как толщину интерметаллических соединений, так и вероятность образования пустот. В качестве альтернативного варианта можно использовать добавки, которые действуют как компенсаторы диффузии. Следует отметить, что уровень микродобавок не изменяет значительно объёмные механические свойства основных сплавов. Наши результаты, основанные на испытаниях на ударопрочность, демонстрируют возможность значительных улучшений надёжности паяных соединений.
Введение
По мере перехода электронной промышленности к бессвинцовой пайке SAC 305 и SAC 405 cтали наиболее распространенными сплавами благодаря самой низкой по сравнению с остальными сплавами температурой плавления, эвтектическому составу, а также хорошим циклическим усталостным характеристикам. Однако, всё же, несмотря на соответствие большинству требований для успешной бессвинцовой пайки нельзя не упомянуть и некоторые сомнения, возникшие по мере увеличения основных характеристик используемых сплавов. Прежде всего, такие сомнения были связаны с различиями в результатах и эффективности процесса. Одновременно с развитием технологий бессвинцовых сплавов во всём мире развился и значительный интерес к производству мобильной электроники. Эти устройства подчёркивали необходимость хорошей устойчивости к ударным нагрузкам, а ведь именно в этой области как у сплава SAC 305, так и у других сплавов SAC с относительно высоким содержанием серебра (Ag) имеются значительные недостатки.
Главная причина слабой скорости деформирования сплавов SAC 305 в сравнении с эвтектическими оловянно-свинцовыми сплавами кроется в объёмных свойствах сплавов. Большинство бессвинцовых припоев содержат большое количество олова, а содержание серебра и меди составляет 5% и 1% соответственно. У таких сплавов относительно высокая прочность и эластичность, но более низкое полное акустическое сопротивление, поэтому при ударных нагрузках больше вероятность передачи напряжений границам раздела между припоем и подложкой. Интерметаллические соединения (IMC), формирующиеся в процессе пайки, имеют малую вязкость, поэтому именно на данной границе раздела и возникает хрупкий излом при тестировании на ударопрочность.
В качестве замены SAC-сплавам с высоким содержанием серебра, использующихся в корпусах BGA и CSP, предлагалось большое число проверенных и широко обсуждаемых в специальной литературе сплавов. Первым учитываемым фактором являются объёмные свойства сплава. Эффект увеличения прочности сплавов с высоким содержанием олова можно минимизировать посредством выбора сплавов с малым содержанием серебра. При снижении содержания серебра в сплаве становится меньше интерметаллических соединений Ag3Sn и, следовательно, уменьшается механическая прочность. На рисунке 1 показана прочность на сдвиг семейства сплавов SAC. Сплавы с меньшим содержанием серебра имеют преимущество в потенциальном снижении эффекта высокой скорости деформации.
Рис. 1. Механические свойства серебросодержащих сплавов SAC
Вторым изученным фактором является происхождение и количество образующихся в процессе пайки интерметаллических соединений (IMC). Данная область более сложная. Высокая скорость образования хрупких изломов может проявиться при пайке бессвинцовым припоем на всех подложках, включая OSP Cu, ENIG, матовые Ni и подложки с плёнками (Au/Ni), нанесённые распылением. Образуемые пограничные интерметаллические соединения определяются синхронными фазами (свободной энергией) припоя с высоким содержанием олова и подложки таким образом, что, например, при пайке SAC-сплавом Cu6Sn5 будет синхронной фазой на границе раздела между припоем и подложкой, а Cu3Sn соответственно в равновесии с подложкой. Качество образованных интерметаллических соединений зависит от времени пайки, температуры и последующих условий старения компонентов. Вероятность хрупкого излома определенной границы раздела зависит от состава интерметаллического соединения, например, из двух бинарных интерметаллических соединений CuSn Cu3Sn более хрупок и отличается также толщиной интерметаллического соединения и наличием таких дефектов, как поры Киркендалла, медленно развивающиеся трещины и остаточное напряжение между слоями интерметаллических соединений, например, (Ni,Cu)6Sn5 и (Ni,Cu)3Sn4 [2,3]. Увеличения стойкости к ударным нагрузкам можно добиться контролем, как за начальным образованием интерметаллических соединений, так и за их последующим развитием в течение срока службы устройства, включая дефекты интерметаллических соединений.
В ходе работ по улучшению характеристик припоев компания Cookson Electronics исследовала вязкость SAC-сплавов с низким содержанием серебра, улучшенными свойствами смачивания и растекаемости, включая модификацию и контроль за интерметаллическими соединениями посредством преобразования и комбинирования микросплавных добавок.
В данном исследовании сравнивается производительность семейства сплавов SAC как с содержащими микродобавки запатентованными сплавами SACX, так и со сплавами SACX без микродобавок. Роль серебра и меди в сплавах SAC напрямую зависит от Cu6Sn5 и Ag3Sn, упрочняющие матрицу Sn. Снижение содержания серебра и поддержание уровня содержания меди для контроля за растворением подложки, а также добавление висмута (Bi) для улучшения характеристик смачивания и усталостной прочности [4] составили основу сплава для развития микродобавок.
В процессе обсуждения влияния микросплавных добавок на изменение процесса развития интерметаллических соединений установлена прямая зависимость соединений от самих добавок. Так, И.Андерсон вместе с другими специалистами [5] указывает на улучшения в структуре хрупкого излома SAC-сплавов при добавлении кобальта (Co) и железа (Fe) с учётом снижения скорости растворения меди из подложки. При этом снижается вероятность образования как хрупкой фазы Cu3Sn, так и пустот. Ф. Гао [6] в процессе обсуждения данного вопроса говорит о похожей реактивной диффузии при добавлении кобальта и никеля (Ni) на базе термодинамических моделей и делает вывод о том, что кобальт и никель обладают большим сродством с оловом, чем с медью и их разветвление может образовать Cu6Sn5 посредством зарождения и роста Cu3Sn. В отсутствии добавок к переходным металлам диффузия по границам зёрен может привести к значительному росту интерметаллических соединений. Степень блокирования роста Cu3Sn при добавлении небольшого количества никеля показана на рисунке 2.
Рис. 2. Образование интерметаллических соединений у сплавов SAC305 и SAC3DS + 0,1% Ni
Параллельно компания Cookson создала ряд бессвинцовых сплавов на оловянно-цинковой основе (SnZn) с низкой температурой пайки [7]. Наличие в составе этих сплавов микродобавок в виде индия (In), никеля, железа и кобальта оказалось эффективным при модификации эвтектического состава, целью которой было уменьшение содержания цинка для улучшения коррозионной устойчивости и образования высокомобильных диффундирующих веществ, например, индия, которые действуют как «компенсаторы» диффузии, минимизируя поры Киркендалла у паяных соединений, образованных с использованием сплавов олово - цинк — медь.
В данной работе показан процесс относительной деформации у SAC-сплавов с низким содержанием серебра при комбинированном добавлении висмута, никеля, хрома (Cr), германия (Ge) и индия. Микродобавки выбирались с целью оптимизации объёмных характеристик сплава, изменения особенностей образования интерметаллических соединений и улучшения характеристик окисления припойного сплава.
Ход испытаний
Испытания проводились на установках для тестирования соединений Dage 4000 и Dage 4000 HS. Установка Dage 4000 способна выполнять проверку шариковых выводов на целостность и надёжность со скоростью до 15 мм/сек, а Dage 4000 HS выполняет аналогичную процедуру со скоростью до 1000 мм/сек. Все испытания проводились с использованием сфер размером 18 мил (450 мкм), собранных на подложках типа CABGA100 и сфер размером 12 мил (300 мкм), смонтированных на подложках CBGA84, где для покрытия контактной площадки применялся сплав никель-золото (NiAu). Сферы монтировались с использованием пастообразного водорастворимого флюса (Alpha WS9180-M3), наносившегося на подложки через трафарет. Установка сфер проходила методом простого ручного монтажа и оплавления в среде воздуха в конвекционной печи оплавления, состоящей из семи зон. Два сплава с низким содержанием серебра на основе олово-серебро-медь (SAC105: Sn1,0Ag0,5Cu) и SACX: Sn0,3Ag0,7Cu0,1Bi), а также обычные SAC-сплавы SAC405 и SAC305 для сравнения использовались с рядом микродобавок. Образцы, не прошедшие испытания, сгруппированы в соответствии с выявленным дефектом, как показано на рисунке 3.
Рис. 3. Режимы отказа шариковых выводов при растяжении. Изображения со сканирующего электронного микроскопа
Режим 1 – Дефект контактной площадки. Контактная площадка отслаивается от подложки, что указывает на плохое качество платы или подложки.
Режим 2 – Дефект шарикового вывода. Наиболее распространённая неисправность, которая указывает на вязкое разрушение паяльного материала.
Режим 3 – Экструзия шарикового вывода. Возникает из-за неправильного расположения используемого для монтажа инструмента или по причине чрезмерной твёрдости припоя.
Режим 4 – Неисправность стыковых или интерметаллических соединений. Дефект образуется на границе между припоем и контактной площадкой. Данная неисправность может иметь большее максимальное значение силы и преимущественно проявляется как хрупкий излом.
Высокоскоростное испытание на деформацию
Испытания на ударную прочность проводились в соответствии со стандартом JEDEC JESD22-B111, применяемым для определения воздействия ударной нагрузки на электронные мобильные устройства [8]. Однако данный метод испытаний требует много времени и затрат. На корпусах BGA и CSP для оценки качества паяной сферы можно использовать метод проверки на растяжение и на срез. В процессе испытаний удалось показать, что высокая скорость среза и высокая скорость деформации шарикового вывода, определённые тестером DAGE 4000 HS , имитируют воздействие ударной нагрузки [9, 10]. Помимо воздействия высокой температурой (150ºC) и увеличения количества фаз интерметаллических соединений стандартные испытания на растяжение и срез с помощью тестера DAGE 4000 могут воспроизводить результаты испытаний на удар.
В данном исследовании упоминается комбинация высокоскоростных испытаний на растяжение и на удар на узлах типа CABGA100 с использованием оборудования для испытаний на удар от компании Lansmont (рис. 4).
Рис. 4. Система испытаний на ударную прочность и протокол испытаний по стандарту JEDEC
В дополнение к высокоскоростным испытаниям на растяжение и ударную нагрузку также исследовались характеристики смачивания и растекания сплавов. Сферы размером 12 мил помещались на флюс, нанесенный методом трафаретной печати на образец для испытаний, предварительно покрытый органическим защитным покрытием. Затем в воздушной среде конвекционной печи, состоящей из семи рабочих зон, проведено оплавление. Тестовые образцы с органическим защитным покрытием использовались для улучшения смачиваемости. После оплавления образцы погружались в горячую воду для удаления твёрдых остатков флюса. В процессе оплавления припой смачивает поверхность и растекается. Затем измеряется область смачиваемой поверхности и определяется коэффициент растекаемости как относительное увеличение в области, относящейся к выступающему поперечному сечению сферы.
Результаты
В программе развития свойств сплавов компанией Cookson Electronics проведено множество испытаний микросплавных SAC-припоев. Выбранные данные приведены ниже для демонстрации основных характеристик припоя, кинетики роста интерметаллических соединений, а также паяемости с учетом растекаемости и стойкости сплава к потускнению.
Состав SAC-сплавов
На рисунке 5 приведены данные испытаний на удар с использованием сплавов SAC405, SAC305, SAC105 и SACX на компонентах типа CABGA100, смонтированных со сферами размером 18 мил. Сплавы с высоким содержанием серебра на низких циклах склоны к большему числу неисправностей, чем сплавы с низким содержанием серебра. Как показано выше на рисунке 1, дефект возникает из-за низкого модуля припойного сплава и является важным фактором в выборе паяльных сплавов для высокоскоростных применений.
Рис. 5. Испытания стандартных SAC-сплавов на удар
Эффект микросплавных добавок
В этой работе показывается большое число легирующих добавок, но при этом подробнее рассматривается эффект от добавок никеля, хрома, висмута, германия и индия. Данный выбор основывается на желании подчеркнуть возможность инженерных комбинаций, направленных на улучшение свойств сплавов с учётом той роли, которую играют микродобавки и интерметаллические соединения в процессе пайки и при тестировании.
Роль висмута
Компания Cookson разработала серию SAC-сплавов с улучшенной смачиваемостью и растеканием. Одним из компонентов этих сплавов является висмут. Так как ряд авторов [11, 12] ранее уже обсуждал вопрос влияния висмута на вероятность хрупкого излома, то нашей целью являлось определение производительности модифицированных висмутовых SAC-сплавов при испытании на растяжение и ударную нагрузку.
На рисунках 6 и 7 показаны результаты испытаний как на сплавах SAC305, SAC205, SAC105, SAC0307 (SACX без висмута), так и на аналогичных сплавах с содержанием висмута 0.1%. Тестирование проводилось на чипах типа CABGA100 со сферами 18 мил. После оплавления и перед выполнением испытания на растяжение компоненты подвергались резкому перепаду температуры (150ºС) в течение 500 часов. Скорости испытания – 15 мм/сек – оказалось достаточно для обнаружения хрупкого излома (режим 4) на приработанных паяльных узлах.
Рис. 6. Испытания шариковых выводов на деформацию с использованием SAC-сплава при добавлении 0,1% висмута и без висмута
На рисунке 7 показаны результаты испытаний для SAC-сплавов как с добавлением висмута, так и без висмута. Коэффициент, равный единице, означает отсутствие эффекта после добавления висмута, при этом коэффициент >1 указывает на увеличение дефектов при добавлении висмута, в то время как показатель <1 означает улучшение качества соединений.
Рис. 7. Соотношение отказов в режиме 4 без висмута и при добавлении в SAC-сплавы 0,1% висмута
На рисунках 8 – 11 приведены графики распределения Вейбулла с результатами испытаний на ударную нагрузку при использовании тех же сплавов как с добавлением висмута, так и без. Также как и данные испытаний на растяжение, результаты испытаний на удар показывают отрицательное влияние на результат после добавления висмута в сплавы SAC305 и SAC205, включая незначительное (сплав SAC105) и значительное (сплав SAC0307, SACX0307+0,1Bi) улучшение качества соединений.
Рис. 8. График Вейбулла для сплавов SAC305 без висмута и SAC305 с добавлением 0,1% висмута
Рис. 9. График Вейбулла для сплавов SAC205 без висмута и SAC205 с добавлением 0,1% висмута
Рис. 10. График Вейбулла для сплавов SAC105 без висмута и SAC105 с добавлением 0,1% висмута
Рис. 11. График Вейбулла для сплава SAC0307 и SACX
Высокоскоростные испытания на деформацию шариковых выводов (при скорости 1000 мм/сек) на компонентах CBGA84 со сферами размером 12 мил с использованием припоя SACX при разных уровнях добавок висмута показаны на рисунке 12. В дополнение к отказам в приведённом режиме 4 на рисунке точками отмечен уровень растекаемости припоя. Число отказов режима 4 уменьшается с увеличением уровня содержания висмута, при этом увеличивается уровень растекаемости припоя.
Рис. 12. Высокоскоростное испытание на деформацию с использованием сплава SACX с разными уровнями добавок висмута
Таким образом, влияние добавок висмута на отказ реакции деформации в паяных соединениях в значительной степени зависит от сплава. Очевидное уменьшение хрупких изломов в режиме 4 наблюдается только у сплавов с низким содержанием серебра (Ag <1%). Значительные улучшения отмечаются у тех сплавов SACX (Ag = 0,3%), в которых содержание висмута составляет не более 2%. На рисунке 12 показано, что снижение числа хрупких изломов по мере увеличения содержания висмута сопровождается также улучшением смачиваемости и растекаемости сплава.
Роль никеля и хрома
Никель и хром не являются распространёнными добавками к SAC-сплавам, однако потенциальное влияние этих добавок на микроструктуру сплава и химию поверхности привлекло интерес к их изучению.
Показатели растекаемости сплава SAC105 измерялись различными уровнями добавления никеля, что показано на рисунке 13. Оптимальный уровень содержания никеля для сплава SAC105 составляет 0,05%. Растекаемость при более высоком содержании никеля ухудшается из-за образования оксидов никеля. Тем не менее, хорошая растекаемость наблюдается при увеличении уровня содержания никеля в сплаве SACX до 0,1%.
Рис. 13. Растекаемость припоя из сплава SAC105
На рисунке 13 также показаны результаты теста на деформацию шарикового вывода при разных добавках никеля. Между улучшенной деформацией и растекаемостью припоя существует взаимозависимость. Содержание никеля 0,05% является оптимальным значением. То же самое подтверждается тестом на ударную нагрузку, приведенным на рисунке 14.
Результаты испытаний на удар для сплава SAC105 с содержанием никеля 0,05% и 0,5% приведены на рисунке 14. Производительность при содержании никеля 0,5% значительно ниже, чем при 0,05%. Данный вопрос обсуждается ниже с учётом интерметаллических соединений, образующихся при пайке сплавами с более высоким содержанием никеля.
Рис. 14. Результаты испытаний сплава SAC10S на удар (с добавлением 0,05% и 0,5% никеля)
Рис. 15. Сравнение результатов испытаний на ударную нагрузку. (SACX без никеля и SACX с добавлением 0,1% никеля)
Рисунок 15 показывает результаты испытаний при использовании в сплаве SACX 0,1% никеля. В этом случае в испытании на удар можно заметить лишь незначительное улучшение.
Добавление хрома оказывает отрицательное влияние на растекаемость припоя. Однако в сочетании с никелем можно заметить улучшение растекаемости. На рисунке 16 показано взаимодействие уровней никеля и хрома в сплаве SAC105. Несмотря на то, что данное взаимодействие довольно сильное, возможна дальнейшая оптимизация данной связи.
Рис. 16. Растекаемость припоя из сплава SAC105 при добавлении никеля и хрома
Добавление никеля и хрома наиболее эффективно сказывается на механических свойствах сплавов. На указанном выше рисунке 2 показано влияние нанесенного на медное защитное покрытие содержащегося в сплаве SAC305 никеля (0,1%) на рост слоя интерметаллического соединения Cu3Sn в процессе обработке при температуре 150°С. Добавление никеля практически уменьшает вдвое образование хрупких интерметаллических соединений при испытаниях на старение паяных соединений в течение 500 часов. При этом улучшается эффективность высокоскоростного испытания на деформирование как можно видеть ниже на графиках распределения Вейбулла и по результатам испытания на растяжение шариковых выводов.
На рисунке 17 приводится сравнение тестов на ударную нагрузку для сплава SAC105 с добавлением никеля и сплава SAC105 с добавлениями никеля и хрома.
Рис. 17. Результаты испытаний сплавов на удар (SAC105 с добавлением 0,1% никеля и SAC105 с добавлением 0,1% никеля и 0,03% хрома)
На рисунке 18 показаны результаты высокоскоростного испытания на растяжение для сплава SAC105 с добавлением никеля и хрома.
Рис. 18. Результаты высокоскоростных испытаний шариковых выводов на деформацию (SAC105, SAC105 с добавлением 0,1% никеля, SAC105 с добавлением 0,03% хрома и SAC105 с добавлением 0,1% никеля и 0,03% хрома) хрома и SAC105 с добавлением 0,1% никеля и 0,03% хрома)
При наличии в сплаве SAC105 0,05% никеля при высокоскоростном испытании на растяжение в режиме 4 обнаружено примерно на 30% меньше отказов по сравнению со сплавом SAC105 без добавок. Аналогичным образом добавление в состав сплава SAC105 0,1% и 0,5% никеля приводит, соответственно, к снижению примерно на 15% – 20% числа отказов по сравнению со сплавом SAC105 без добавок.
Добавление 0,03% хрома в сплав SAC105 уменьшает число дефектов примерно на 40%. Важно отметить, что между никелем и хромом по аналогии с результатами растекаемости припоя возникает синергический эффект. Значительное улучшение качества паяных соединений обеспечивает уже одно только добавление хрома (0,03%), а добавление в сплав никеля (0,1%) приводит к снижению количества хрупких изломов при испытаниях в вышеупомянутом режиме 4. Коллективный эффект от добавления никеля и хрома значительнее, чем сумма индивидуальных эффектов.
Роль германия, индия и никеля
По разным причинам германий с никелем не являются самыми распространёнными добавками к бессвинцовым припоям. Оба элемента дорогостоящие при том, что германий слабо растворяется при взаимодействии с оловом. Тем не менее, индий обладает хорошим свойством как компенсатор диффузии, а германий может улучшить структуру поверхности. Несмотря на то, что значительные улучшения растекаемости и смачиваемости припоя при добавлении германия и индия не выявлены, тем не менее, в ходе испытаний на деформацию и удар удалось определить некоторые улучшения. Графики 19 и 20 объединяют полученные данные.
Рис. 19. Высокоскоростные испытания шариковых выводов на деформацию (сплав SACX с различными добавками)
Как показано на графике 19, при высокоскоростном испытании на деформирование шарикового вывода сплава SACX с содержанием никеля 0.05% выявлено примерно на 50% меньше отказов, чем у немодифицированного сплава SACX. В то же самое время добавление 0,05% германия увеличивает этот показатель более чем на 50%. Добавление 0,05% индия снижает число отказов приблизительно на 30%, в то время как результаты испытаний при наличии 0,5% никеля показывают неизменное по сравнению с немодифицированным сплавом SACX число дефектов.
Интересно, что в отличие от SACX добавление 0,05% германия в сплав SAC105 уменьшает на 20% число вероятных отказов при высокоскоростном испытании на расстяжение.
На рисунке 20 показаны результаты сравнения испытания на удар для сплава SACX с добавлением германия, никеля и индия.
Рис. 20. Сравнение результатов испытаний на удар (SACX с добавлением никеля, германия и индия)
Устойчивость к потускнению
На рисунке 21 показано изменение цвета сферы в результате термообработки. Испытания проводились сначала в течение 12 часов при температуре 125°С, затем в течение 168 часов при температуре 85°С и относительной влажности 85%. После этого следовало три цикла оплавления при температуре 255°С, включая 30 секунд оплавления свыше 217°С. Сферы основного сплава SAC305 без обработки поверхности приняли коричневатый оттенок. Добавление небольшого количества (~50 мкг/г) фосфора устраняет проблему, однако сферы по-прежнему принимают желтоватый оттенок. Окончательно избавиться от дефекта помогает добавление в сплав SAC305 хрома. Следует также отметить, что добавление никеля также обеспечивает хорошую защиту от потускнения.
Рис. 21. Влияние добавок на устойчивость сфер к потускнению (Термообработка в течение 12 часов при температуре 125°С; 168 часов при OB 85% и температуре 85°С; оплавление в воздушной среде при температуре 255°С)
Исследование
Эффект от добавления висмута
Результат добавления в бессвинцовые сплавы висмута рассматривается во многих исследованиях. Наличие висмута может как снизить температуру солидуса, улучшить прочность паяных соединений посредством дисперсионного уплотнения, так и замедлить образование больших интерметаллических соединений Ag3Sn в основном припое [11]. Результаты испытаний также показывают распределение висмута к границе между медным покрытием и интерметаллическими соединениями [12]. Несмотря на замедление роста интерметаллических соединений возможно образование хрупких изломов.
Результаты этой работы показывают существенное влияние висмута. Так, в частности, добавление до 2% висмута в SAC-сплавы улучшает смачивание и растекаемость сплава. Растекаемость сплава улучшается при последующем добавлении 0,005 – 0,05% висмута. Хорошие свойства растекаемости можно объяснить поверхностной сегрегацией микросплавных добавок. Так как висмут не образует интерметаллического соединения с медью, то высокая концентрация висмута на границе между припоем и медной подложкой способствует лучшей растекаемости сплава. То же самое можно сказать и про другие переходные металлы, которые неохотно образуют интерметаллические фазы при взаимодействии с медью при нормальных температурах пайки.
Роль висмута в отказах при высокоскоростных испытаниях деформации зависит от сплава. Добавление висмута в сплавы с высоким содержанием серебра, например, в сплав SAC305, снижает прочность при воздействии ударных нагрузок, см. рис. 8. С уменьшением содержания серебра вероятность проявления негативного эффекта снижается. Добавление висмута в сплав SACX (0,3% серебра) увеличивает стойкость соединений к растяжению и воздействию ударной нагрузки, что показано на рисунках 8 – 11.
По результатам испытаний Д. Шан [13] указывает на то что, добавление висмута замедляет рост интерметаллического соединения и может служить границей между медью и интерметаллическим соединением. Так как сплав с высоким содержанием серебра переносит напряжение к границе интерметаллического соединения, то качество паяного соединения при добавлении висмута значительно не улучшается.
И, наоборот, благодаря более низкому модулю у SAC-сплавов с низким содержанием серебра поддерживается необходимый уровень интерметаллических соединений при добавлении висмута без риска образования хрупких изломов. SAC105 (1% серебра) является промежуточным звеном между отрицательным и положительным влиянием висмута на высокоскоростное испытание на растяжение.
Эффект от добавления никеля и хрома
Эффект от добавления небольшого количества никеля в SAC-сплавы описывается несколькими авторами, например, Пером-Эриком Тэгехоллом [14]. Одновременно с увеличением хрупкости у Cu6Sn5 наличие никеля также замедляет рост интерметаллических соединений при термической обработке (150°С) , как показано на рисунке 2.
В нашем испытании никель оказывает сильное влияние на рост интерметаллического соединения, и при добавлении 0,05% уменьшается на треть число отказов у сплава SAC105 при растяжении шариковых выводов в вышеприведённом режиме 4. Для сплава SACX этот показатель снижается вдвое. Более высокие уровни содержания никеля менее эффективны при испытаниях на растяжение несмотря на более высокую скорость роста интерметаллических соединений при пайке [15].
Наряду с увеличением скорости деформирования никель обладает двумя другими преимуществами. При оптимальном уровне добавления (~0,05%) SAC-сплавы с никелем отличаются улучшенной растекаемостью припоя, как показано на рисунке 13. Кроме этого, никель также обеспечивает значительное улучшение стойкости к потускнению, что необходимо учитывать при монтаже корпусов типа BGA и CSP.
Хром не растворяется при контакте с оловом, поэтому довольно сложно добиться оптимального результата при добавлении хрома в сплавы SAC. В данном исследовании нашей целью был поиск возможности снижения значения модуля или абсолютной величины деформации припоя наряду с увеличением стойкости к потускнению. При малой скорости деформирования шарикового вывода при использовании SAC-сплава с добавлением 0,03% хрома заметно снижение предела прочности на разрыв по сравнению со сплавом без микродобавок. Мы можем рассматривать это как эффект сплавления хрома. Хром сплавляется через компонент меди в припое, ограничивая при этом образование интерметаллического соединения Cu6Sn5 в припое. Кроме этого, при высокоскоростном испытании на деформирование число отказов у сплава SAC105 с содержанием 0,03% хрома снижается примерно на 40%, как показано на рисунке 18.
Однако, самым значительным открытием является обнаружение того, что хром при взаимодействии с никелем способствуют уменьшению образования дефектов (режим 4) более чем на 80%. Результаты испытаний на удар воспроизведены на рисунке 17.
Эффект от добавления германия в SAC-сплавы
Влияние содержания германия в сплавах изучено на предмет улучшенных коррозионных характеристик в сочетании с улучшениями механических свойств. Результаты высокоскоростного испытания на растяжение при добавлении только 0,05% германия менее успешны чем ожидалось. Так, например, число отказов при использовании германия в сплаве SACX возросло на одну треть.
Эффект от добавления индия в SAC-сплавы
В качестве добавки к SAC-сплавам индий снижает вероятность образования пор Киркендалла, но слабо влияет на рост интерметаллического соединения Cu3Sn [16]. Роль индия как «компенсатора» диффузии подкреплена созданием компанией Cookson оловянно-цинковых бессвинцовых сплавов. В то же самое время М. Амагаи [16] и другие специалисты полагают, что наличие индия в SAC-сплавах эффективно влияет на снижение дефектов растяжения шариковых выводов. Что же касается сплавов SACX, то качество паяных соединений можно улучшить только при добавлении индия к никелю или к составному сплаву никель+хром. Следует отметить также, что в настоящее время для поддержки представленных в данном исследовании феноменологических данных специалистами проводится подробный анализ причин возникновения отказов, изучается кинетика роста интерметаллического соединения для сплавов с микродобавками индия, а также определяется эволюция сплавов и их промежуточных микроструктур.
Заключение
Высокоскоростное испытание семейства бессвинцовых сплавов SAC c микросплавными добавками на деформирование проведено для определения пригодности сплавов к сборке корпусов типа BGA и CSP. Результаты проведенных высокоскоростных испытаний на растяжение шариковых выводов не только соответствуют стандартным результатам испытаний на ударную прочность промышленных стандартов, но и также демонстрируют значительное улучшение прочности соединений по сравнению с немодифицированными SAC-сплавами.
По результатам испытаний сделаны следующие заключения:
- SAC-сплавы с низким содержанием серебра более устойчивы к деформированию при ударных нагрузках.
- Ряд микросплавных добавок улучшает ударную прочность соединений, в особенности сочетание никель+хром обеспечивает соединению хорошую ударопрочность и устойчивость к потускнению.
- Добавление висмута и никеля улучшает на 20% растекаемость припоя на органическом защитном покрытии из меди. Улучшение поддерживается и для комбинации висмут+никель+хром.
- Наилучшая комбинация свойств наблюдается при использовании модифицированных сплавов SAC105 и SACX с добавлением 0,05% никеля и 0,03% хрома.
- При использовании в сплавах с низким содержанием серебра (Ag <1%) висмут улучшает стойкость к ударным нагрузкам и характеристики деформации. При высоком содержании серебра в SAC-сплавах добавление висмута отрицательно влияет на деформацию.
- Незначительные добавки индия снижают на 30% число отказов в ходе высокоскоростных испытаний на растяжение у всех SAC-сплавов. Добавление индия в SAC-сплавы не влияет на растекаемость и смачивание сплавов.
Список использованных источников:
- Yoshiharu Kariya et al. J. of Elect. Mat, 33, No.4, 2004
- C.E. Ho, Y. W. Lin, S. C. Yang and C. R. Kao, Volume Effect on the Soldering Reaction between SnAgCu and Ni, Proc. IEEE/CPMT 10th Int. Symp. On Advanced Packaging Materials, 2005
- T. Gregorich, P. Holmes, J. C. B. Lee and C. C. Lee, SnNi and SnNiCu Solders, Proc. IPC/Soldertec Global 2nd Int. Conf. On Lead Free Electronics, 2004
- Patents Applied, Aug. 2005
- I. E. Anderson and J. L. Harringa, Ames Lab Iowa, J. elect. Mat. 32, p.1485, 2004
- F. Gao, T. Takemoto and H. Nishikawa, Effects of Co and Ni addition on reactive diffusion between SnAg solder and Cu during soldering and annealing, Mat. Sci. Eng., A420, 30-46, 2006
- Patent Applied, Feb. 2007
- JEDEC Solid State Technology Association, JESD22B111: “Board Level Drop Test Method of Component for Handheld Electronics Products”, 2003
- K. Newman, “BGA Brittle Fracture – Alternative Solder Joint Integrity Test Methods,” Proc. 55Th Electronic Components and Technology Conf., Orlando, FL, May-June 2005, pp. 1194-1201
- R. Pandher and M. Boureghda, “Identification of Brittle Solder Joints using High Strain Rate Testing of BGA Solder Joints” to be Presented at International Reliability Symposium, Phoenix, April 15-19, 2007
- M. L. Huang and L. Wang, Effects of Cu, Bi and In on Microstructure and Tensile Properties of SnAg-X (Cu, Bi, In) Solders, Met. And Mat. Trans., 36A, 6, p1439, 2005
- P. L. Liu and J. K. Shang, Interfacial Segregation of Bismuth in Cu/Sn-Bi Solder Interconnect, Scripta Met. 44, p1019, 2001
- J. K. Shang, P. L. Liu and C. Z. Liu, Bismuth Segregation at SnCu Reactive Interfaces, Proc. Mat. Sci. and Tech. Conf., New Orleans, 2004
- Per-Erik Tegehall, IVF Project Report (ELFNET), March 2006
- J. Y. Tsai, Y. C. hu, C. M. Tsai and C. R. Kao, A Study of the Reaction between Cu and SnAg doped with small amounts of Ni, J. Elect. Mat.32, No 11, p1203, 2003
- M. Amagai, Y. Toyoda, t. Ohnishi and S. Akita, High Drop Test Reliability: Lead Free Solders, Proc. 54Th ECTC, p1304, 2004
Статья была ранее опубликована на сайте elinform.ru
Понравилась статья? Поставьте лайк
Электроника Производство электроники Поверхностный монтаж (SMT) Пайка оплавлением Бессвинцовая пайка Монтаж штыревых компонентов (THT) Пайка волной Бессвинцовая пайка
Читайте также
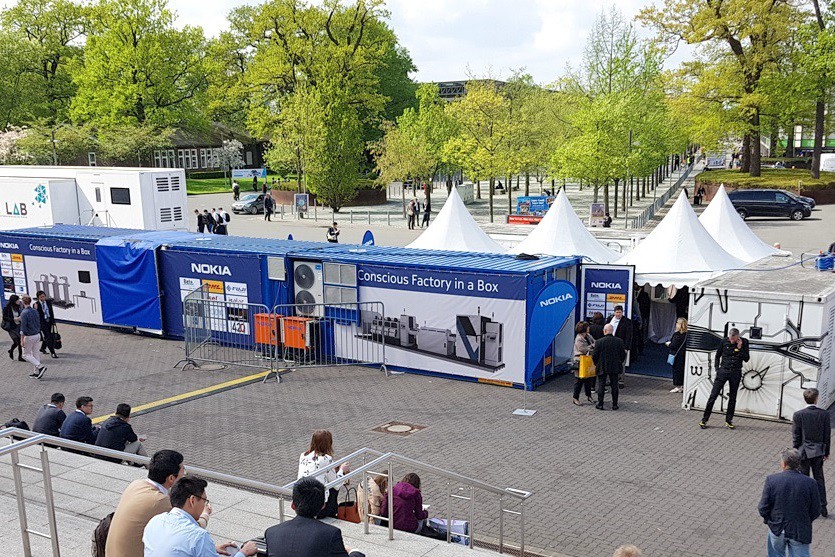
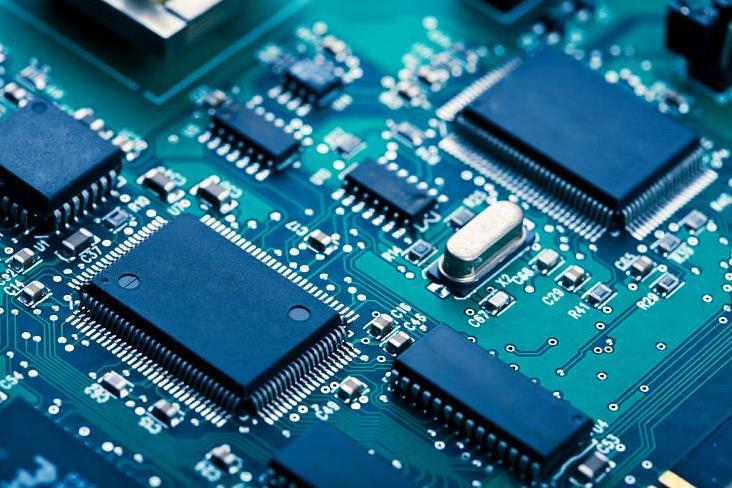
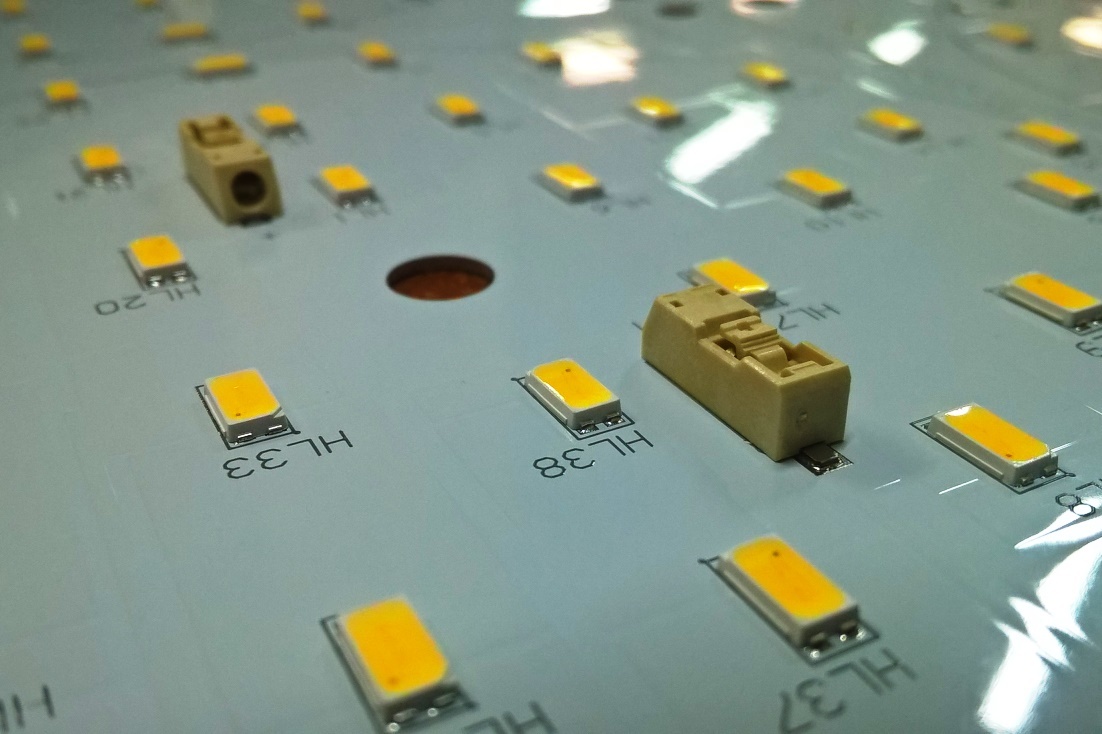