Здесь мы собираем самые интересные статьи, интервью, репортажи и многое другое.
Азот при оплавлении: нужен или нет? Мы провели эксперимент и говорим: нужен!
Павел Константинов, konstantinov@microem.ru Ольга Жиляева, olga.zhilyaeva@airliquide.com
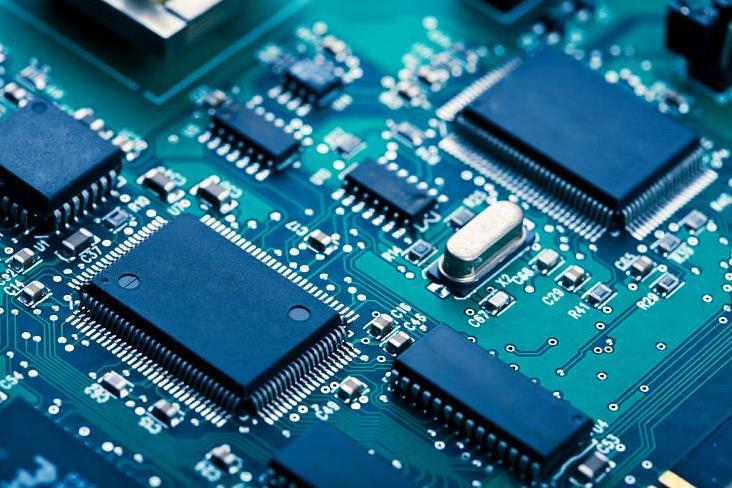
Конкуренция в современном мире диктует жесткие правила экономии. Они приводят к использованию менее затратных технологий и более дешевых материалов, что в финале становится причиной снижения качества электронных изделий. К счастью, есть много производителей, которые заинтересованы в том, чтобы их продукция не просто работала, а делала это долго и надежно. Именно для таких взыскательных заказчиков лучшие контрактные производители могут предложить пайку в азотной среде.
Все основные плюсы и минусы оплавления в среде азота широко известны, материалов по этой теме много. В статье будут рассмотрены дополнительные преимущества, реализованные на контрактном производстве «МикроЭМ Технологии» благодаря применению в процессе оплавления азота от компании Air Liquide.
Технологическое окно и влияние на надежность паяного соединения
Базовое отличие для технологии среды азота от атмосферы при оплавлении заключается в низкой концентрации кислорода; по данным исследований REHM Thermal systems, эффективным является уровень содержания кислорода 500 ppm и меньше [1]. Из-за низкого содержания кислорода в процессе оплавления поверхность выводов компонентов и контактных площадок печатных плат (рабочие поверхности пайки) практически не окисляются. Поскольку рабочая поверхность пайки содержит меньше окислов, а следовательно, она «чище», то для ее активации до нужного уровня потребуется меньшая активность флюса, что при тех же технологических материалах означает меньшие пиковые температуры профиля оплавления. Получается, что использование среды азота при оплавлении расширяет его технологическое окно. Особенно актуально это при использовании бессвинцовых паяльных материалов, когда температуры на плате и компонентах доходят до +260 °C.
Практикум
Нами были проведены продолжительные исследования расширения технологического окна оплавления, при этом использовались современные материалы: паяльная паста на основе припоя Rel61 (аналог SAC305) с температурой плавления +208…+215 °C [2]. Эксперименты подтвердили, что применение инертной среды азота позволяет уменьшить пиковые температуры в точках оплавления вплоть до +230 °C.
По результатам исследований была выполнена корректировка профиля оплавления с уменьшением пиковой температуры при использовании азота на тестовых бессвинцовых изделиях. В «азотной версии» базового бессвинцового профиля оплавления температура на плате была снижена на 7–10 °C (в зависимости от изделий) по сравнению с «атмосферной версией» того же профиля, причем характеристики паяных соединений остались на высоком уровне.
С использованием азота пайка стала более блестящей визуально (рис. 1), количество пустот в паяных соединениях не изменилось (рис. 2). На рис. 1 видно, что при оплавлении в среде азота вся контактная площадка на печатной плате (1) оплавлена, а площадка на компоненте (2) сохранила блестящий цвет, в атмосферной же среде площадка на плате не оплавлена по периметру, а площадка на компоненте утратила блеск. Один из наглядных результатов показан также на рис. 3 — наличие торцевой галтели на корпусах типа QFN, при оплавлении в азоте она явно выражена, в отличие от оплавления в атмосфере.
Рис. 1. Визуальное отличие оплавления в среде азота от атмосферного оплавления (бессвинцовые материалы). Отличия рабочих поверхностей пайки: 1 — смачивание углов контактной площадки на плате; 2 — состояние контактной площадки компонента
Рис. 2. Анализ пустот в паяных соединениях изделия: а) оплавление в азоте; б) оплавление в атмосфере
Рис. 3. Результат 3D-инспекции корпуса типа QFN: а) оплавление в азоте; б) оплавление в атмосфере При оплавлении в азоте торцевая галтель явно выражена, при оплавлении в атмосфере она заметно меньше либо отсутствует
Кроме того, по данным совместных исследований компании Air Liquide и Osaka University, оплавление в среде азота не только уменьшает вероятность образования дефекта «оловянные усы» [3], но и позволяет избежать характерного дефекта «надгробных камней», если подобрать соответствующие технологические режимы [1].
Таким образом, при оплавлении с использованием азота и надежность пайки увеличивается, и визуальный контроль (в том числе и на установках АОИ) становится проще.
Влияние на компоненты
Уменьшение пиковой температуры при оплавлении снизило негативное влияние на компоненты, входящие в состав изделия. Для оценки были проведены исследования влияния на емкостные характеристики поверхностно монтируемых алюминиевых электролитических конденсаторов, как одних из самых чувствительных компонентов. Зарубежные исследования по этой тематике подтверждают: в отличие от традиционной свинцовой технологии при пайке по бессвинцовой технологии возможны и обоснованы массовые отказы алюминиевых электролитических конденсаторов [4].
Производители компонентов также предупреждают об изменениях емкости при на рушении рекомендованного термопрофиля свыше 50% [5, 6]. Безусловно, производители перестраховываются с цифрами, однако суть понятна.
Практикум
Кратко о методике:
- Выбраны современные компоненты известного производителя, номинал 330 мкФ, корпус 10×10,2 мм (CaseG).
- Маркировка и измерение стартовых показателей емкости компонентов.
- Размещение в заданном порядке на тестовых платах различной толщины.
- Прохождение в печи по исследуемым температурным профилям — имитация теплового воздействия при пайке (рис. 4, 5).
- Измерение емкости после первого оплавления.
- Имитация повторного оплавления и повторное измерение емкости.
Рис. 4. Термопрофиль пайки тестируемого изделия в воздушной среде
Рис. 5. Термопрофиль пайки тестируемого изделия в среде азота
Результаты:
- «Атмосферный» термопрофиль — уменьшение емкости от первоначальных значений на 2,5% после оплавления и 3,5% после двух оплавлений.
- «Азотный» термопрофиль — уменьшение емкости от первоначальных значений на 1,8% после оплавления и 2,5% после двух оплавлений.
Конденсатор можно считать исправным, пока его емкость не уменьшится на 20% [8], зависимость снижения емкости от времени близка к прямой линии для 330 мкФ (рис. 6). В этом случае разница 0,7% емкости (рассматривать будем единичное оплавление), обеспеченная лишь смягчением термопрофиля, условно может интерпретироваться как 3,5% его времени жизни. Время жизни при работе в жестких условиях эксплуатации хороших современных электролитических конденсаторов (~+100 °C) это приблизительно 6000 ч, а потому полученные 3,5% времени жизни составляют 210 ч. Соответственно, для менее жестких условий такое значение будет увеличиваться для +50 °C увеличение времени жизни составит 210×25 = 6720 ч, уже существенное значение.
Рис. 6. Падение емкости электролитических конденсаторов от времени [7], красным цветом выделен исследуемый номинал
Таким образом, мы считаем, что использование азотной среды и соответствующего термопрофиля смягчило воздействие на компоненты и продлило время жизни электролитических конденсаторов на 6720 ч усредненного использования.
Влияние на печатную плату
Под воздействием высоких температур пайки базовые материалы печатной платы также повреждаются, внешне об этом свидетельствуют изменение цвета, расслоение, провисание. Температура разложения стандартного стеклотекстолита около +320 °C, это заметно выше пиковых температур оплавления [9]. Расслоение печатных плат в нашей практике — единичные случаи на «давальческих» платах, связанные с нарушением технологии производства изготовителями печатных плат и носят несистемный характер. Базовый материал печатных плат под действием высоких температур размягчается. При температурах пайки разрушения стеклотекстолита не происходит, поэтому чем сильнее тепловое воздействие, тем сильнее размягчается материал. Оценить степень размягчения можно по величине провисания платы при ее фиксации с торцов и под воздействием температуры относительно нормального состояния. Поэтому для оценки разницы влияния «азотного» и «атмосферного» температурного профилей на материал печатной платы, пусть и косвенной, был выбран дефект провисания. При этом в процессе оплавления должна отсутствовать сетчатая и центральная поддержка в печи, для большей наглядности тестовые платы должны быть тоньше, с большим числом линий продольного скрайбирования.
Практикум
- Выбор тестовых плат из серийных изделий, склонных к деформации.
- Прохождение в печи по исследуемым температурным профилям — имитация теплового воздействия при пайке.
- Измерение величины деформации изгиба [10].
В качестве тестовой использовали двухсторонние платы: материал FR-4, размер 200×150 мм, толщина 1 мм, пять продольных рядов в панели, разделенных скрайбом. Выбор такой платы сделан для наглядности, центральная цепная поддержка в печи при этом была отключена (рис. 7). По результатам в среднем на «атмосферном» термопрофиле величина изгиба 7,1 мм, а на «азотном» 5,25 мм. Относительное уменьшение изгиба на ~26%, следовательно, считаем, что использование азотной среды при оплавлении и соответствующего термопрофиля смягчило воздействие на материал печатной платы на условную величину 26%.
Рис. 7. Образец тестовой платы в ходе экспериментов, после оплавления
По нашему опыту, при увеличении пиковых температур оплавления свыше +230 °C отрицательное воздействие на компоненты и печатную плату растет значительно быстрее, чем вызвавший его рост температуры. Поэтому даже небольшое увеличение технологического окна с использованием азотной среды при оплавлении позволяет сгладить температурное воздействие на электронные узлы, особенно актуальное для бессвинцовой технологии.
Напоминаем, что при жестких требованиях далеко не в каждом изделии будут сходиться описанные условия. Однако бывает полезно иметь подобные технологические резервы при изготовлении любых изделий. Особенно если они обязательно проходят процедуру NPI с внедрением всех требований DFM.
Более подробно о решениях компании AirLiquide
Литература
- Reflow Technology: Fundamentals of Reflow Soldering. Part 2: Reflow Soldering Methods, Dr. Hans Bell.
- REL61LEAD-FREE SOLDER ALLOY Technical data sheet, Aim Solder.
- Baated A., Kim K.-S., Suganuma K., Huang S., Jurcik B., Nozawa S., Ueshima M. Effects of reflow atmosphere and flux on Sn whisker growth of Sn-Ag-Cu solders // Journal of Materials Science: Materials in Electronics. 2010. Vol. 21. Iss. 10,
- Wiest C., Blattau N., Wright J., Schatz R. Robustness of Surface Mount Aluminum Electrolytic Capacitors When Subjected to Lead Free Reflow // Passive component industry. 2005. November/December.
- Soldering Profile and Land Pattern Vishay OS-CON, Type 94SVP Solid Aluminum Capacitors With Organic Semiconductor Electrolyte Surface Mount Chip, Document Number: 90014, Revision: 12-Dec-05.
- SMD Aluminum Electrolytic Capacitors, Reflow Condition, Lelon Electronics Corp. 2011 Verison. www.lelon.com.tw/en/product_list.php
- Panasonic Industrial Company, Surface Mount Type Aluminium Electrolytic Capacitors.
- Lakshminarayanan V., Sriraam N. Thermal stress on capacitors: failure prevention. July 8th, 2014. www.ee.co.za/article/thermal-stress-capacitors-failure-prevention.html
- Медведев А., Можаров В., Мылов Г. Печатные платы. Современное состояние базовых материалов // Печатный монтаж. 2011. № 5.
- Бегер Е. Деформации печатных плат: как их предотвратить на этапе конструирования // Печатный монтаж. 2009. № 1.
Понравилась статья? Поставьте лайк
Электроника Производство электроники Поверхностный монтаж (SMT) Пайка оплавлением Бессвинцовая пайка
Читайте также
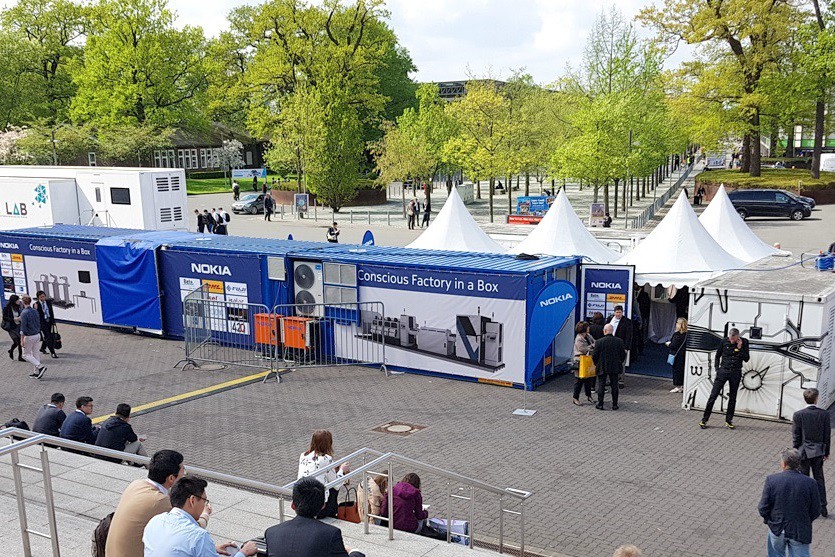
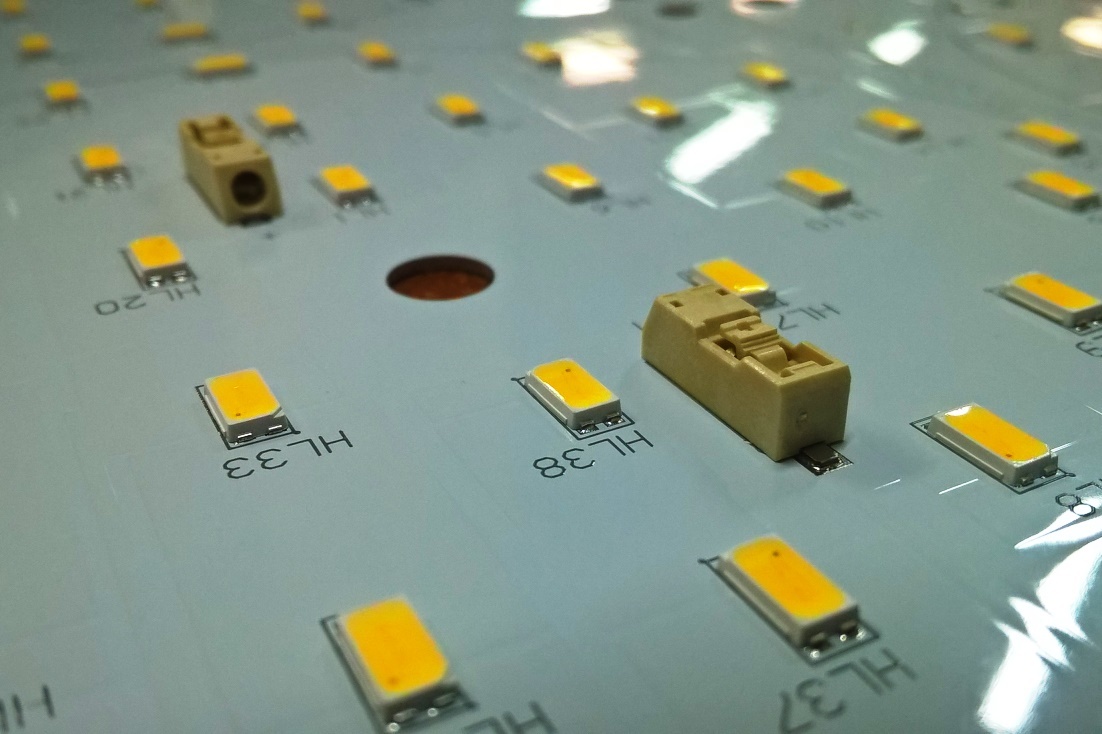
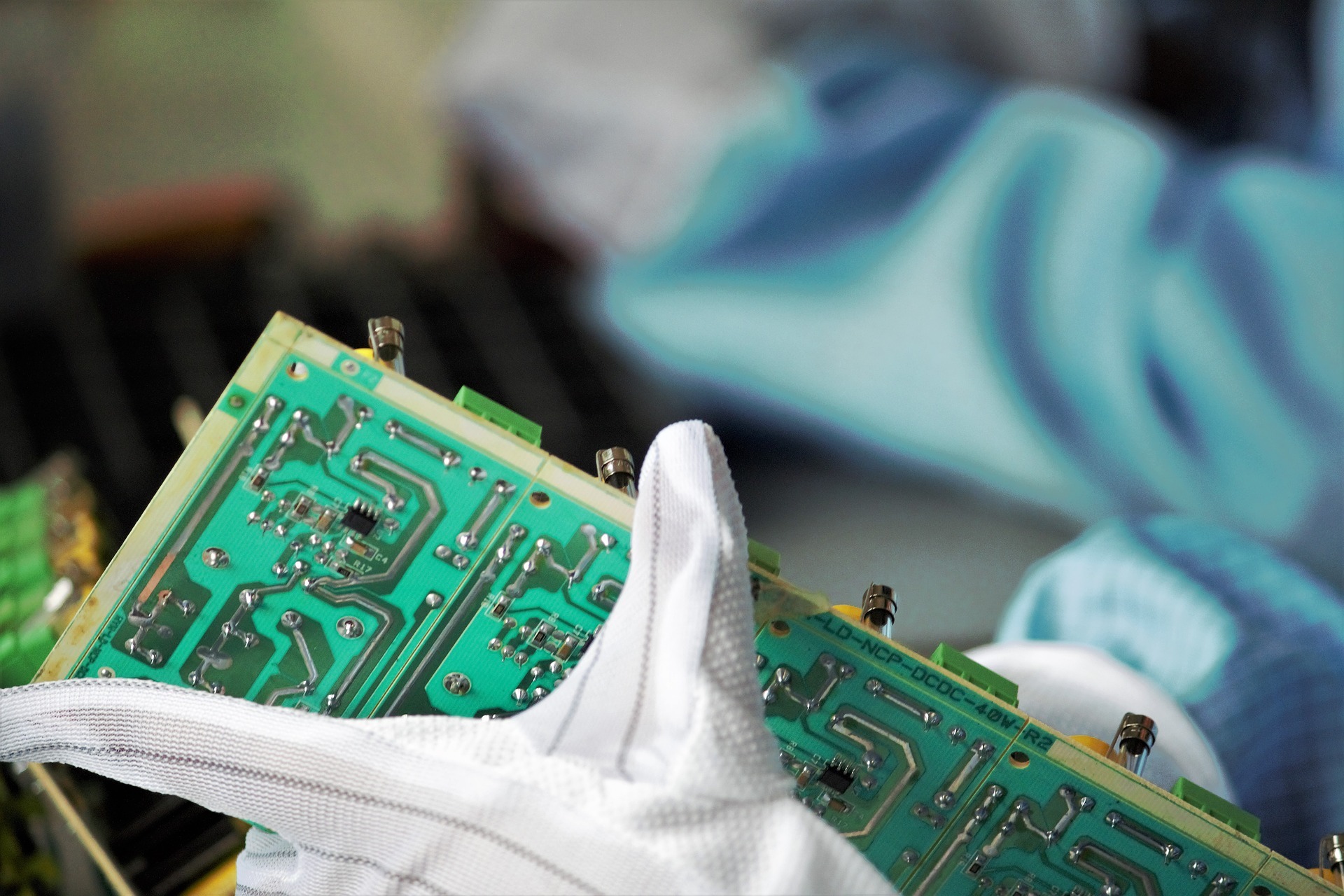